AFRL Collaborative Automation for Manufacturing Systems Laboratory officially opens
WRIGHT-PATTERSON AIR FORCE BASE, OH (AFRL) — The Air Force Research Laboratory, or AFRL, Materials and Manufacturing Directorate celebrated the opening of the Manufacturing, Industrial Technologies and Energy Division’s Collaborative Automation for Manufacturing Systems, or CAMS, Laboratory during a ribbon-cutting ceremony July 23, 2024. The facility will support the research efforts of its Digital Manufacturing Research Team, or DMRT.
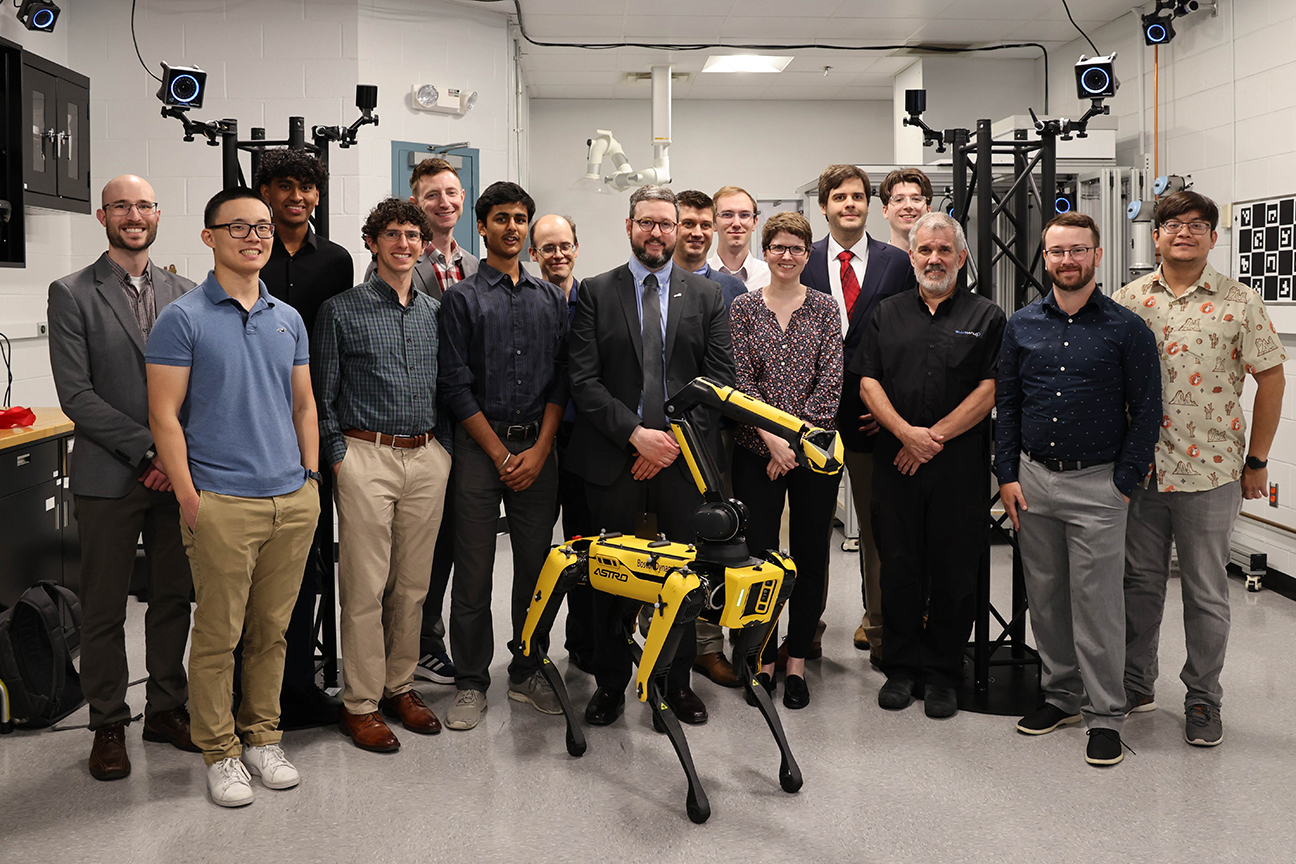
The Air Force Research Laboratory’s Digital Manufacturing Research Team celebrates the official opening of the new Collaborative Automation for Manufacturing Systems Laboratory at Wright-Patterson Air Force Base after a ribbon-cutting ceremony July 23, 2024. This is the team’s first internal laboratory. (U.S. Air Force photo / Sarah Perez)
The CAMS lab is the team’s first internal laboratory and will enhance efforts to research and develop advanced digital manufacturing technology for the Department of the Air Force. These efforts toward digital transformation sync up with the Air Force Material Command’s, or AFMC’s, 2023 AFMC Strategic Plan to deploy Digital Materiel Management, or DMM. DMM leverages digital technology to deliver AFMC’s Organize, Train, and Equip mission.
Ceremony speakers included Timothy Sakulich, executive director of AFRL; Darrell Phillipson, director, AFRL Materials and Manufacturing Directorate; and Dr. Sean Donegan, DMRT lead. They were joined by distinguished visitors Dr. Dan Berrigan, founding DMRT lead, and Nate Ames, executive director of The Ohio State University Center for Design and Manufacturing Excellence.
“I am excited to witness the culmination of these efforts,” said Sakulich. “This vision is about how we look further into the future and posture ourselves to get ahead of where the commercial sector is going to go, and preposition for what the defense sector is going to need.”
Phillipson emphasized the importance of the directorate’s role not only in developing new technology for the warfighter, but also in advancing manufacturing capabilities to ensure it is available whenever and wherever it is needed.
“In the era of the Great Power Competition, AFRL is definitely here to deliver capability and technology, but it’s not enough just to do that,” said Phillipson. “You have to be able to get it out the door. The CAMS Lab will be essential in responding to that need.”
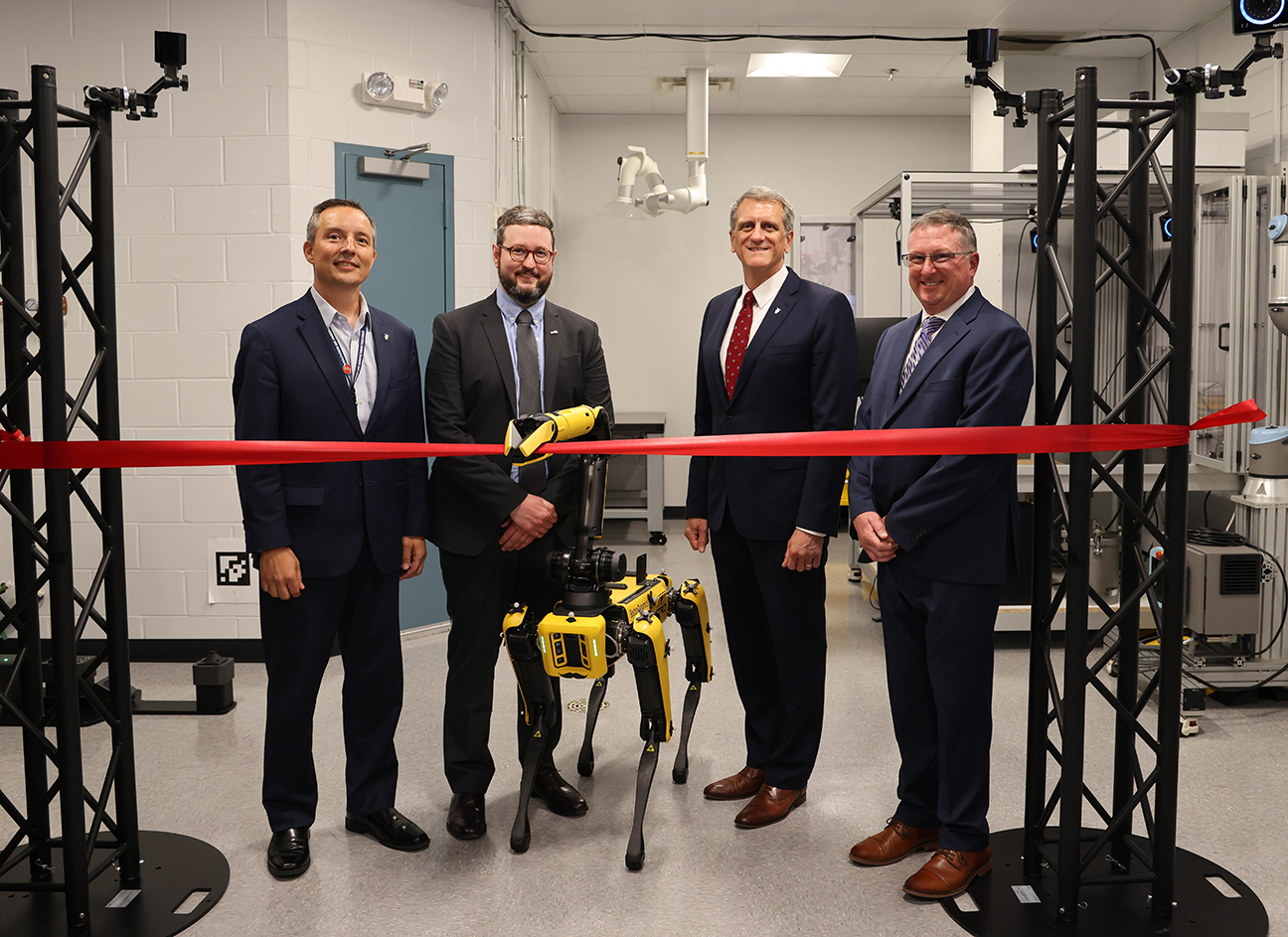
From left: Darrell Phillipson, director, Air Force Research Laboratory, or AFRL, Materials and Manufacturing Directorate; Dr. Sean Donegan, Digital Manufacturing Research Team lead; Timothy Sakulich, AFRL executive director; and Dr. Charles Ormsby, Manufacturing, Industrial Technologies and Energy division chief observe as Boston Dynamics robot Astro cuts a ceremonial ribbon, officially opening the new Collaborative Automation for Manufacturing Systems Laboratory at Wright-Patterson Air Force Base, July 23, 2024. (U.S. Air Force photo / Sarah Perez)
Donegan, who served as a driving force behind making the CAMS Laboratory a reality, said he was grateful to his predecessor, Berrigan. He acknowledged Berrigan’s role in laying the foundation by both developing the idea of exactly what it meant to do digital manufacturing research, as well as developing a portfolio of the Air Force’s current needs in this area.
“Our strategic research outlook targets necessities like point-of-need manufacturing and forward-deployed manufacturing assets,” said Donegan. “This technology will enable rapid refitting of systems in the field for quick turnarounds. This allows for resilient basing and agile combat employment.”
Donegan said DMRT’s development as a team went down a long and winding path from navigating the inability to be in the lab during the COVID-19 pandemic, to leveraging partner laboratories to understand what they needed here at AFRL.
“When it was started, the DMRT grew deep connections with external collaborators like The Ohio State University and Georgia Tech., enabling a distributed laboratory,” said Donegan. “However, as the team expanded its research to meet Air Force needs, we realized that there were critical requirements that could not be met externally.”
The CAMS lab is a unique, state-of-the-art facility that not only fulfills those critical requirements but also complements the labs and partnerships that the DMRT has developed over the years, Donegan added.
James Bieryla, director of the AFRL Strategic Partnering Directorate commented that, though the CAMS lab will be an invaluable resource to the DMRT, the importance of collaborations and partnerships cannot be understated.
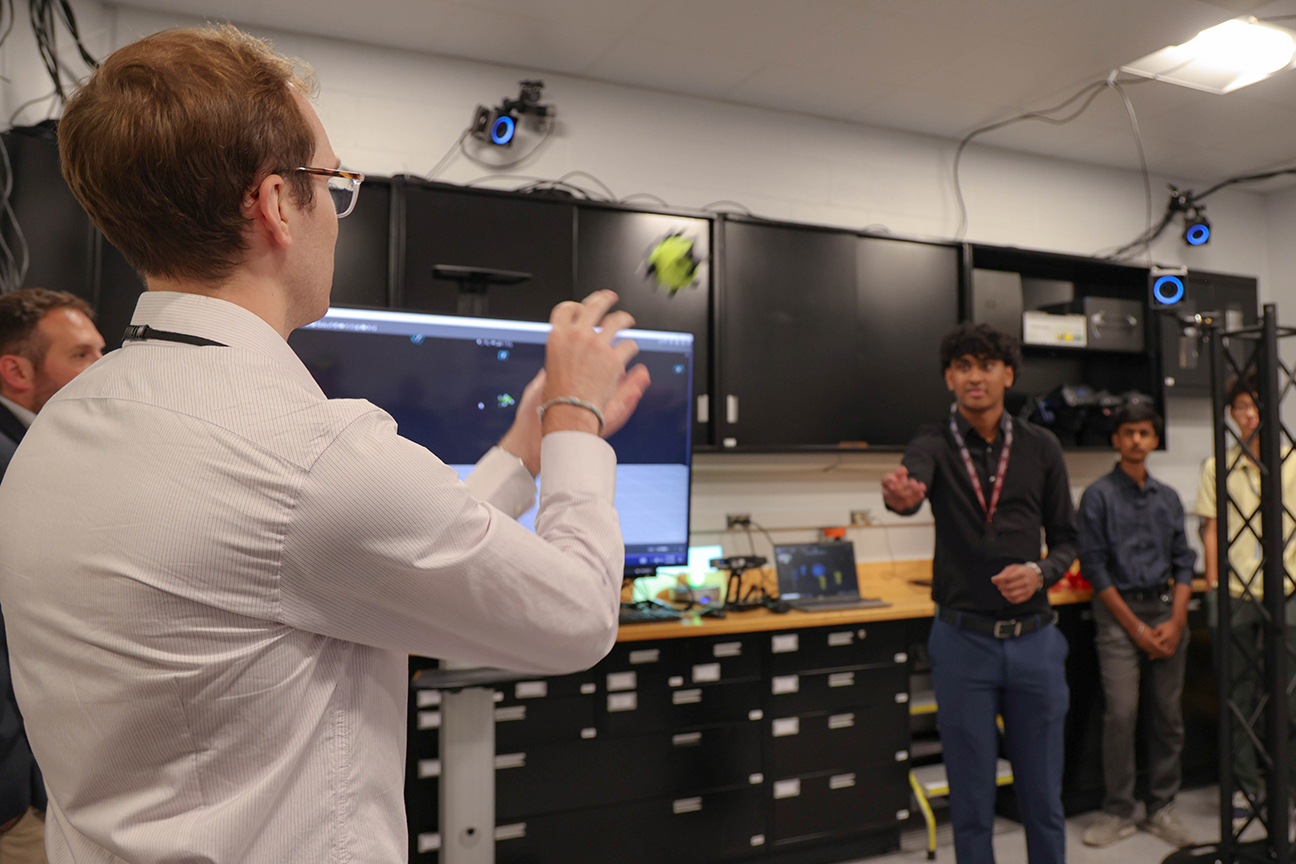
From left: Andrew Bowman, on-site researcher with the Air Force Research Laboratory’s Digital Manufacturing Research Team, or DMRT, and Yash Kakade, a DMRT summer intern, demonstrate the motion capture system in the newly opened Collaborative Automation for Manufacturing Systems Laboratory at Wright-Patterson Air Force Base following a ribbon-cutting ceremony July 23, 2024. (U.S. Air Force photo / Sarah Perez)
“AFRL’s success is equal to the strength of its partnerships,” said Bieryla. “AFRL and its diverse partners develop cutting edge technology together, evolving to become hubs for innovation and key facets for national defense programs.”
Donegan got the ball rolling for the CAMS lab by using money from his own AFRL Early Career Award to provide the cutting-edge robotics hardware, which would not have otherwise been available to the team.
Additionally, Donegan said, the lab also invested in fundamental technology “game changers” that adversaries are also investing heavily in, specifically artificial intelligence and autonomy through robotics.
He said the facility supports several platforms for autonomous manufacturing, including collaborative robotics and industrial extended reality hardware. Donegan said the use of extended reality could help bring additional capability to operators in the field, on the manufacturing line or in the air repair depots to get them back into service.
“We have a big research thrust on how to use augmented and virtual reality to bring additional capability to these operators,” said Donegan. “As an example, when completing a riveting task to put a panel back on a plane, operators would wear an augmented reality headset that would project all of the places that needed a rivet onto the plane.”
Additionally, the lab is fully digitized through a motion capture system which Donegan said is like those used in the video game and movie industries. For the DMRT’s purpose, this system allows for the creation of a digital twin of the laboratory for virtual experimentation in a cloud environment, accelerating manufacturing science through the latest artificial intelligence technologies.
“The definition of digital manufacturing is constantly evolving,” said Donegan. “For us, what it means is, how do we continue to advance manufacturing capabilities for the warfighter? This lab allows us to become expert practitioners in developing those novel capabilities.”
About AFRL
The Air Force Research Laboratory is the primary scientific research and development center for the Department of the Air Force. AFRL plays an integral role in leading the discovery, development, and integration of affordable warfighting technologies for our air, space and cyberspace force. With a workforce of more than 12,500 across nine technology areas and 40 other operations across the globe, AFRL provides a diverse portfolio of science and technology ranging from fundamental to advanced research and technology development. For more information, visit: www.afresearchlab.com.