AFRL helps NASA wrap up equipment testing for Artemis II mission
Editor’s note: This story has been updated to include human testing of the suit and seat from the article originally published May 30, 2023, click here to view.
UPDATE: HUMAN TESTING
In October, the NASA team revisited Wright-Patterson Air Force Base to collaborate with Air Force Research Laboratory, or AFRL, engineers, to further evaluate the latest version of astronaut crew seats and flight suits intended for the Orion spacecraft. Testing was conducted with U.S. Air Force volunteers, who met various height and weight requirements. The testing progressed into November, incorporating human subjects in seat evaluations.
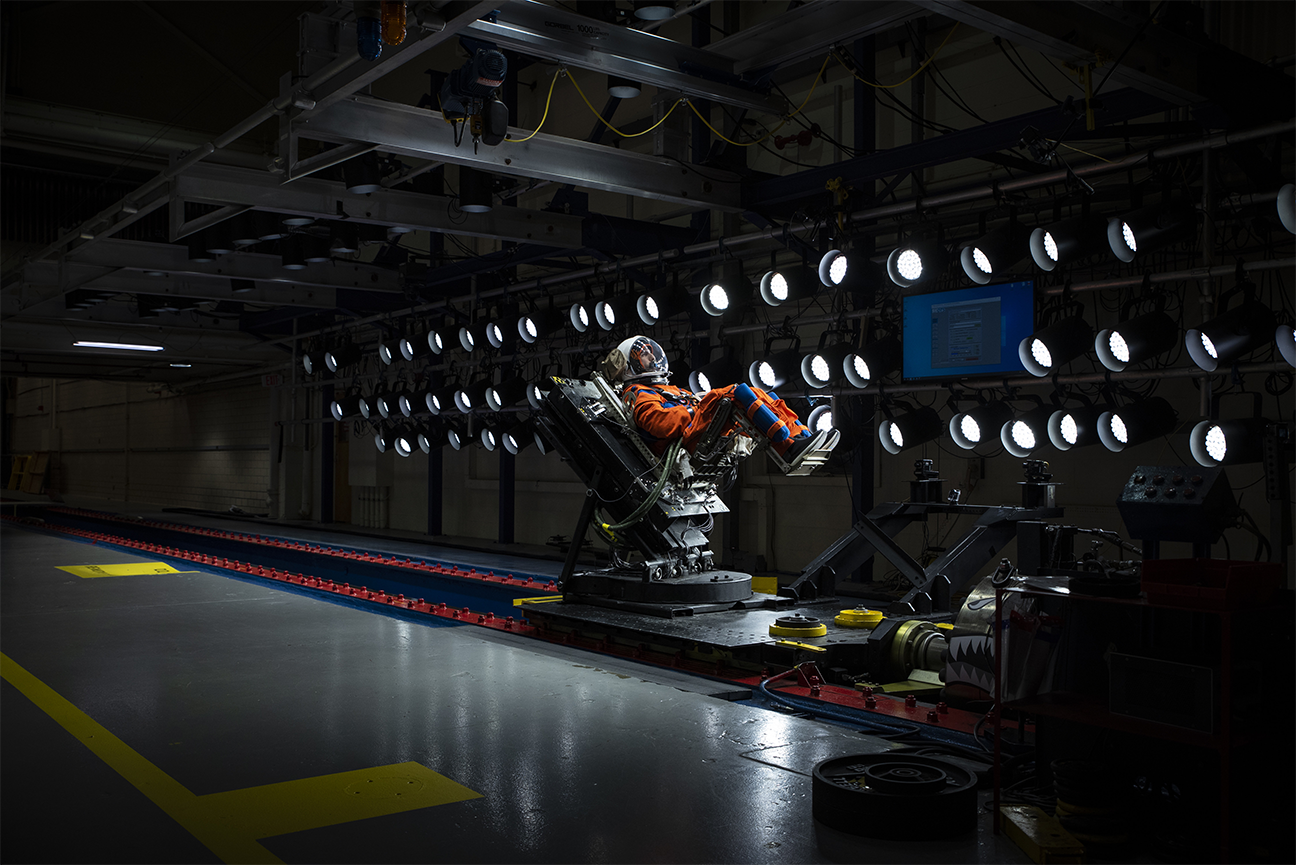
A U.S. Air Force volunteer with the Biodynamics Laboratory tests the next replica of a seat and flight suit for the Orion space capsule and NASA on the horizontal sled test facility at Wright-Patterson Air Force Base, Ohio, Oct. 23, 2023. Researchers with the Air Force Research Laboratory Human Effectiveness Directorate tested equipment for the Orion space capsule’s upcoming mission to the moon. (U.S. Air Force photo / Richard Eldridge)
After concluding the NASA program in April, which centered on integrating the Orion space suit and seat while assessing structural integrity using anthropometric test dummies, or ATDs, for extreme impact predictions, the NASA and biodynamics lab teams started strategizing for their revisit in Fall 2023 to commence trials with human participants, said Chris Perry, senior biomedical engineer, Biodynamics Section, 711th Human Performance Wing.
Conducting human tests enabled the team to collect safety data and receive continuous feedback from the participants, addressing concerns about suit fit, comfort and seat integration during impact events. These tests were performed at impact levels expected during capsule reentry and landing, reflecting more typical experiences.
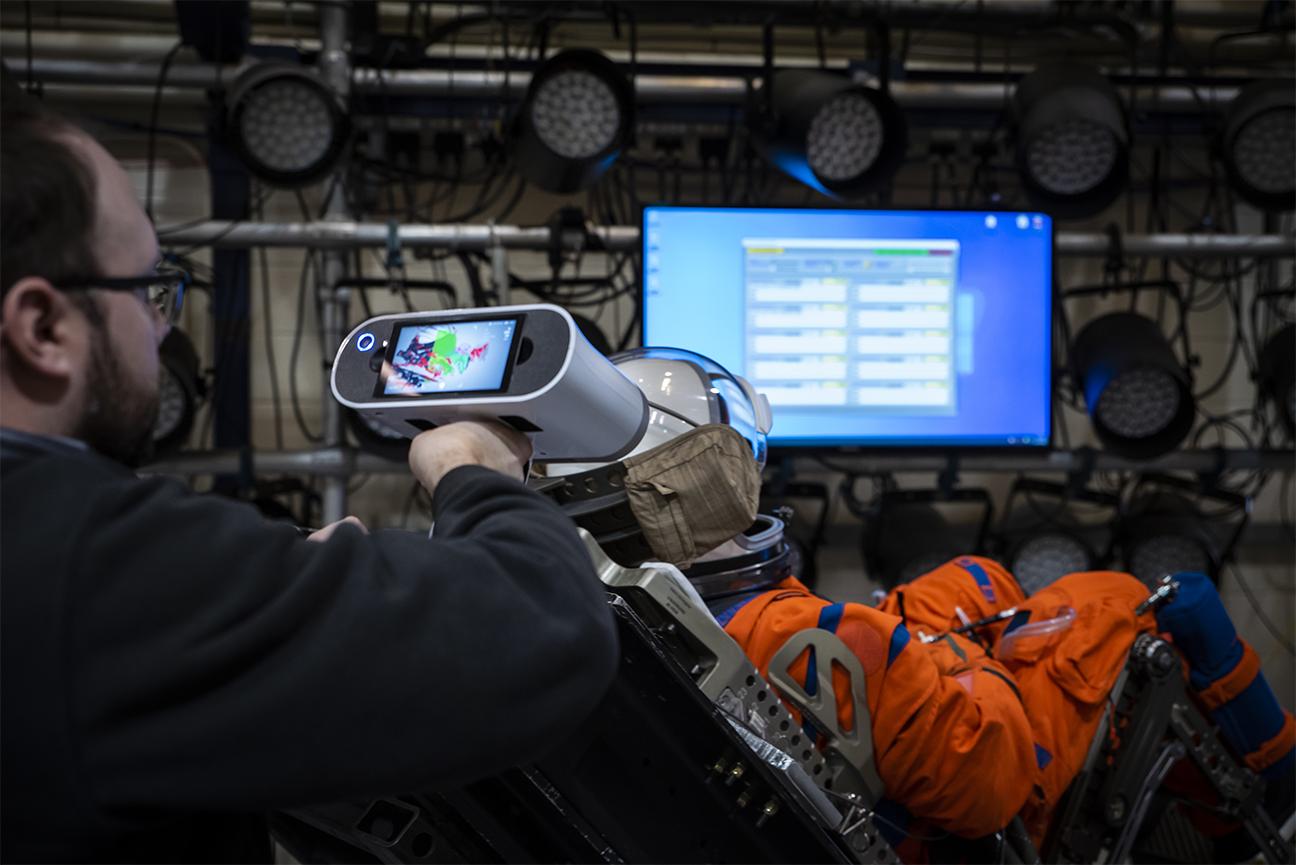
Max Grattan, Biodynamics Laboratory technical support contractor with Infoscitex, conducts 3D surface scanning of a U.S. Air Force volunteer on the horizontal sled test facility at Wright-Patterson Air Force Base, Ohio, Oct. 23, 2023, to test the next replica of a seat and flight suit for the Orion space capsule. Researchers with the AFRL Human Effectiveness Directorate tested equipment for the Orion space capsule’s upcoming mission to the moon. (U.S. Air Force photo / Richard Eldridge)
“Artemis II will be the first operational test of the Orion suit and Orion seat with human occupants,” Perry said.
The ATDs captured intricate metrics encompassing various accelerations, forces and moments, said Dustin Gohmert, Orion crew survival engineer at NASA.
“We can say in this seat with this landing profile, we can compare those recorded metrics to what we know to be safe from other industries, be it a combination of automotive and aerospace,” Gohmert said.
However, due to the inability of ATDs to express comfort or pinpoint areas for minor adjustments, human testing remains essential before the suit can be employed in an actual mission.
Perry highlighted that this testing had three primary objectives.
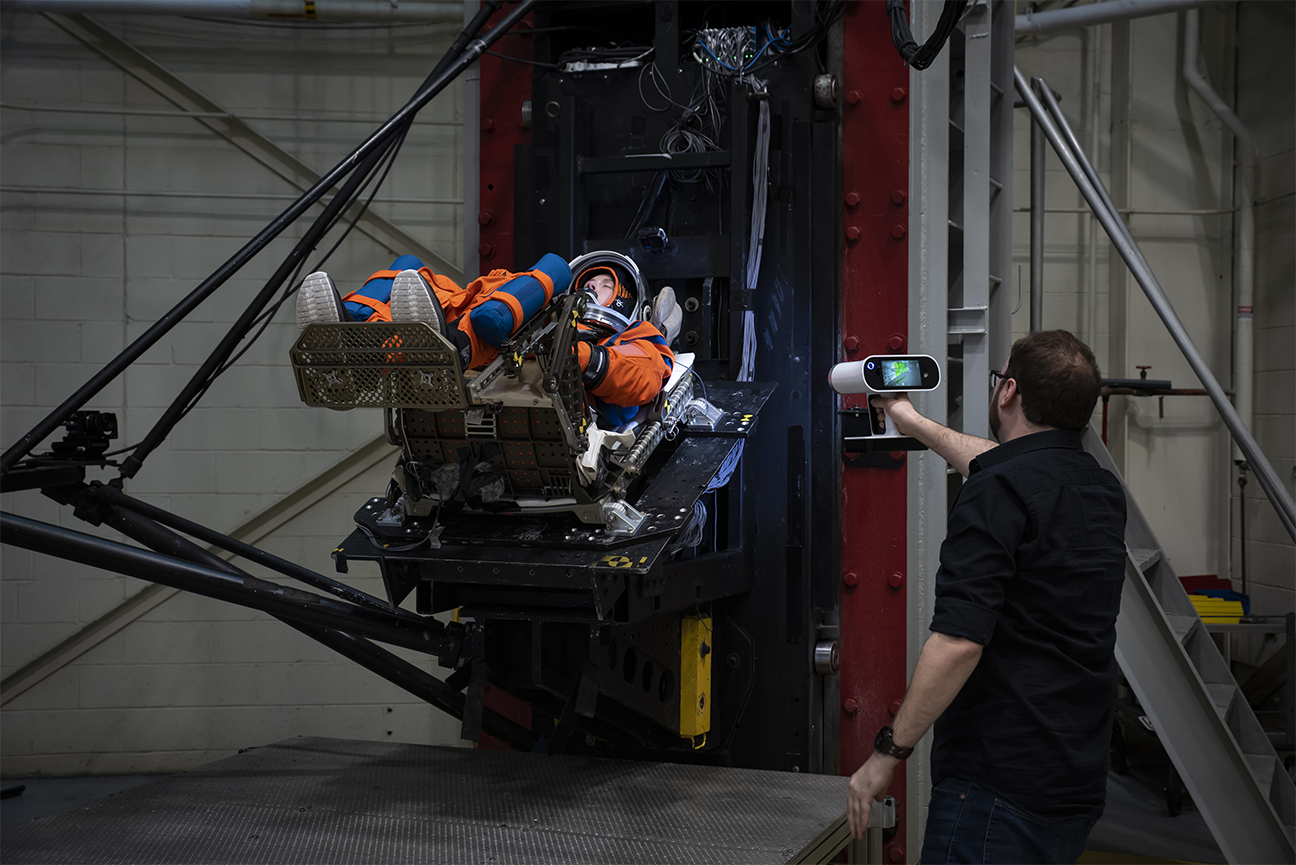
Max Grattan, right, Biodynamics Laboratory technical support contractor with Infoscitex, conducts 3D surface scanning of a U.S. Air Force volunteer on the horizontal sled test facility at Wright-Patterson Air Force Base, Ohio, Nov. 3, 2023, to test the next replica of a seat and flight suit for the Orion space capsule. Researchers with the AFRL Human Effectiveness Directorate tested equipment for the Orion space capsule’s upcoming mission to the moon. (U.S. Air Force photo / Richard Eldridge)
Initially, it aimed to guarantee that the placement of a diverse range of human participants in the seat doesn’t disrupt the restraint system, headrest or equipment during acceleration exposures, potentially elevating injury risks, Perry said. A second goal was to confirm that the interaction between the suit and individuals doesn’t lead to hotspots or soft-tissue injuries during horizontal and vertical impacts. Lastly, it sought to ensure that all participants could brace appropriately in a neutral posture during horizontal and vertical impacts, with their heads against the headrest and shoulders against the seatback.
“The human occupant conforms to suit and the seat in a way the ATD cannot and still provides measured accelerations, which can be used to evaluate safety,” Perry said. “They also can provide a verbal assessment post-test to address the goals.”
Apart from the horizontal tests, the human subjects were also subjected to controlled vertical impact simulations, replicating predictable landing scenarios.
The vertical drop tower replicated the horizontal test’s context, yet it allowed for adjusting the seat orientation concerning how the body is pre-loaded, Gohmert said. The issue lies in aligning with gravity: human positioning in the vehicle, considering the landing acceleration vector, results in a discrepancy in the force of gravity experienced in our testing setup.
“For example, in some of these cases, we’d actually be hanging out of the seat belts,” Gohmert added. “Well, that biases you already away from the seat, which could exacerbate the response. But, on the drop tower, we’re going to actually be laying in the seat and just fall into it, and it really mimics the perfect Orion landing, as we ‘fall on the drop tower to the controlled deceleration.’”
Gohmert said the team was able to match the exact descent seen in Artemis I, which was “the perfect landing,” something he hopes to see in all future landings.
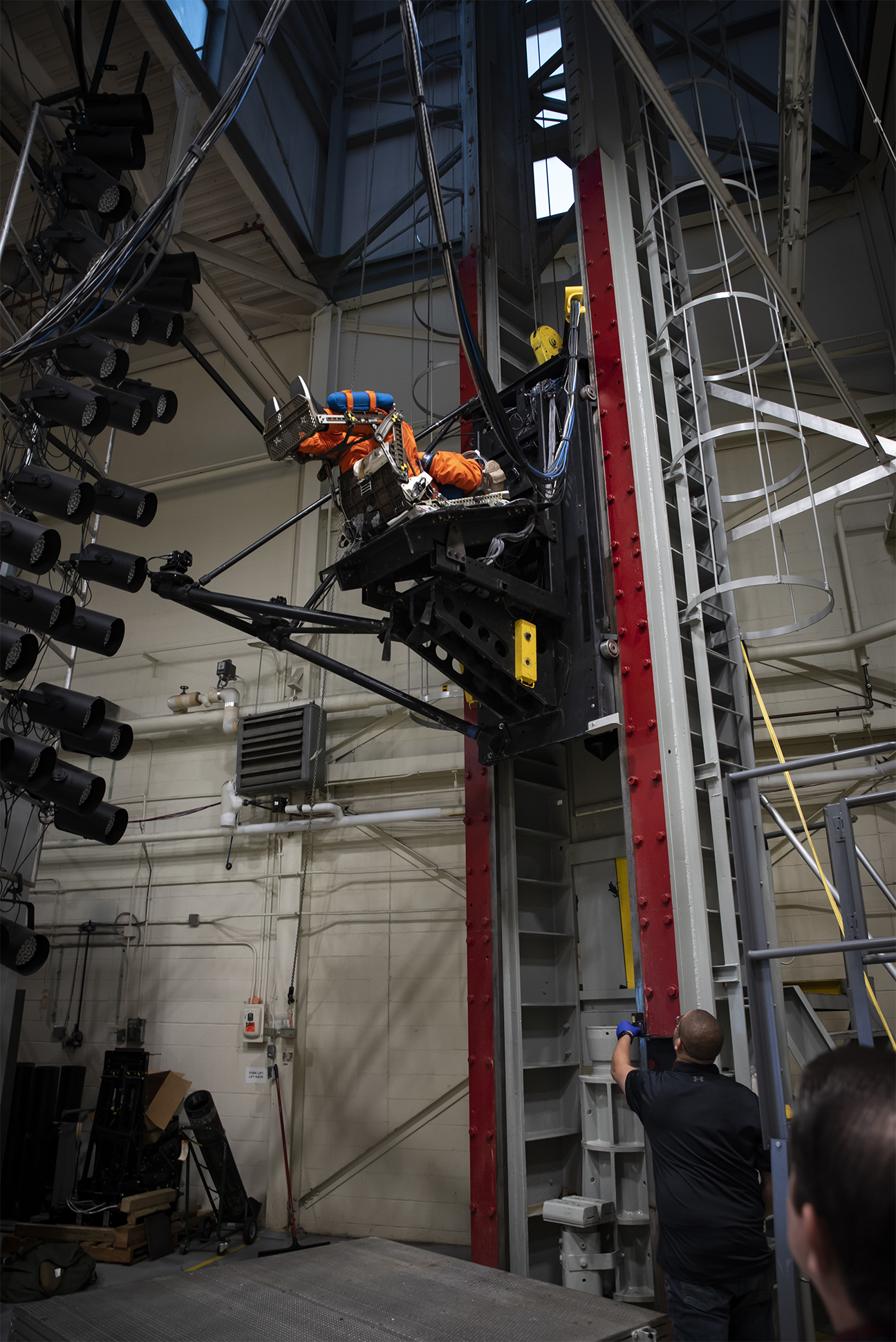
A U.S. Air Force volunteer tests the next replica of a flight suit and seat for the Orion space capsule in the drop tower facility at Wright-Patterson Air Force Base, Ohio, Nov. 3, 2023. Researchers with the Air Force Research Laboratory’s Human Effectiveness Directorate tested equipment along with NASA for the Orion space capsule’s upcoming mission to the moon. (U.S. Air Force photo / Richard Eldridge)
HEARING TESTING
Simultaneously, Hilary Gallagher, a biomedical engineer in AFRL’s Human Effectiveness Directorate, conducted tests on the hearing protection intended to protect the astronauts from the hazardous noise they will be exposed to during launch and re-entry. Twenty individuals underwent testing due to variations in head and ear canal shapes and was fitted twice to observe the variability on the same individual.
Those who have undergone a hearing test are likely familiar with the sequence of sounds heard through a headset in a confined booth.
“This is very similar,” Gallagher said. “But sounds are coming from speakers in the room instead of a headset that you put on.”
The subjects’ track their hearing thresholds across low, mid and high frequencies.
The testing assessed subjects’ natural hearing abilities and while wearing all gear, including communication earbuds, a communications cap and a helmet.
“NASA wants to know how well the astronauts are going to be protected … because it’s very loud for a short time,” Gallagher said. “We’ll apply this data to their noise environment to see how well they’ll be protected.”
WHAT COMES NEXT
Perry and Gohmert both acknowledged that as this trial ended, it carried considerable significance.
“If everything goes well, this will probably be the ultimate test,” Gohmert said. “After being here for over 15 years, this is kind of bittersweet. It may be the last one that we do. Now, I say that with a grain of salt: you never know what’s going to happen next.”
As the human testing wraps up, the testing program will gradually conclude.
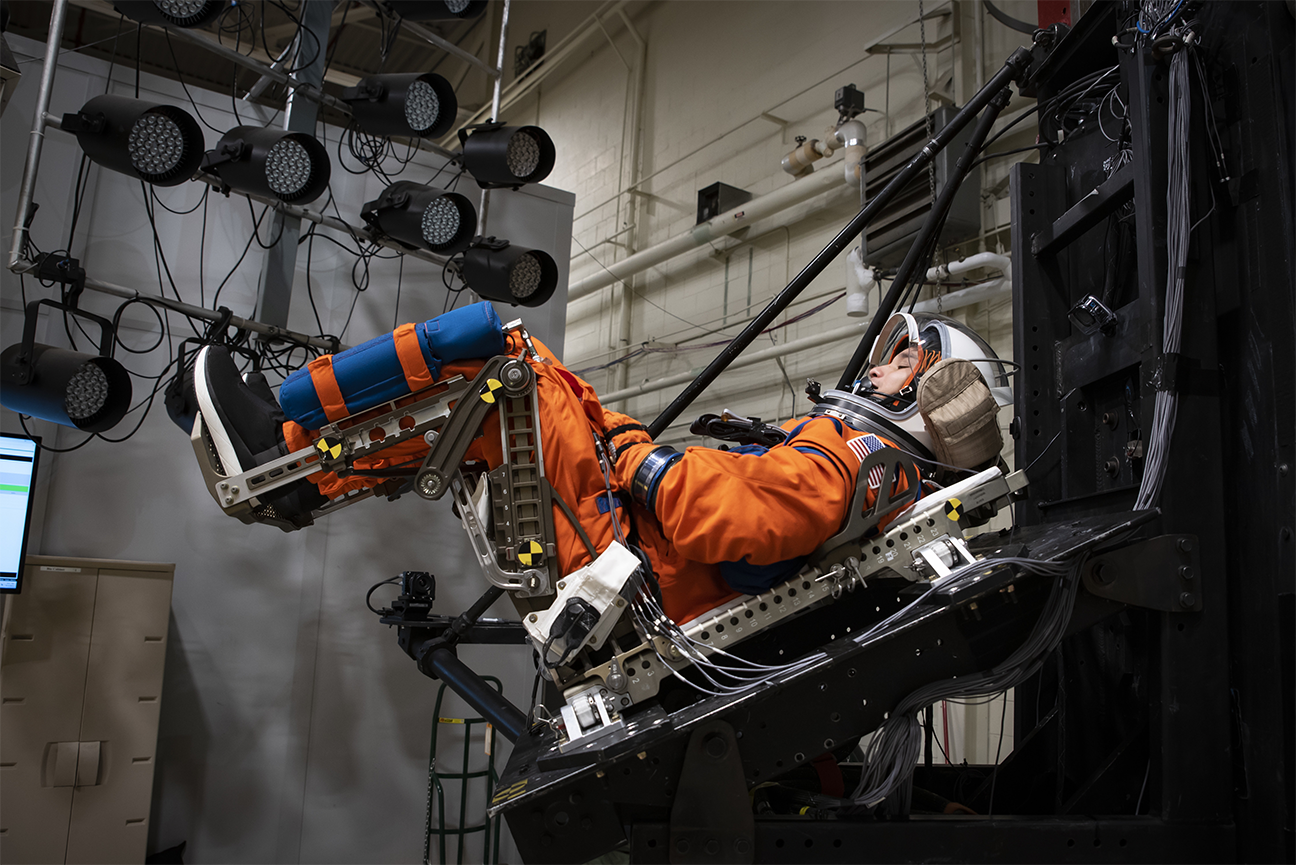
A U.S. Air Force volunteer tests the next replica of a flight suit and seat for the Orion space capsule in the drop tower facility at Wright-Patterson Air Force Base, Ohio, Nov. 3, 2023. Researchers with the Air Force Research Laboratory’s Human Effectiveness Directorate tested equipment along with NASA for the Orion space capsule’s upcoming mission to the moon. (U.S. Air Force photo / Richard Eldridge)
“Sad to say, but at this point, the collaborations we have worked together over the previous 15 years will be winding down for the Artemis program as it relates to the Orion space suit and Orion space capsule seat,” Perry said.
Potential future collaborations might arise during the development of a new lunar landing vehicle, specifically concerning the design of a configuration to restrain occupants, whether in a standing or seated position, he added.
“In the words of one of NASA’s lead engineers on this project, ‘The Orion space capsule and related occupant seat and occupant suit would not be where it is today if not for the collaboration with the Biodynamics Lab at AFRL,’” Perry quoted.
The combined data from both ATDs and human trials collected during previous endeavors have been instrumental in optimizing injury metrics and standards for occupants, Perry said. These findings showed significant alignment between the organizations.
“It was a true collaboration in [every] sense of the word because both NASA and AFRL work to provide the best occupant protection in their respective vehicles,” Perry said. “I look at it this way: optimization of occupant protection and safe systems pushes the envelope to maximize Airman performance and allows them to fly and fight another day.”
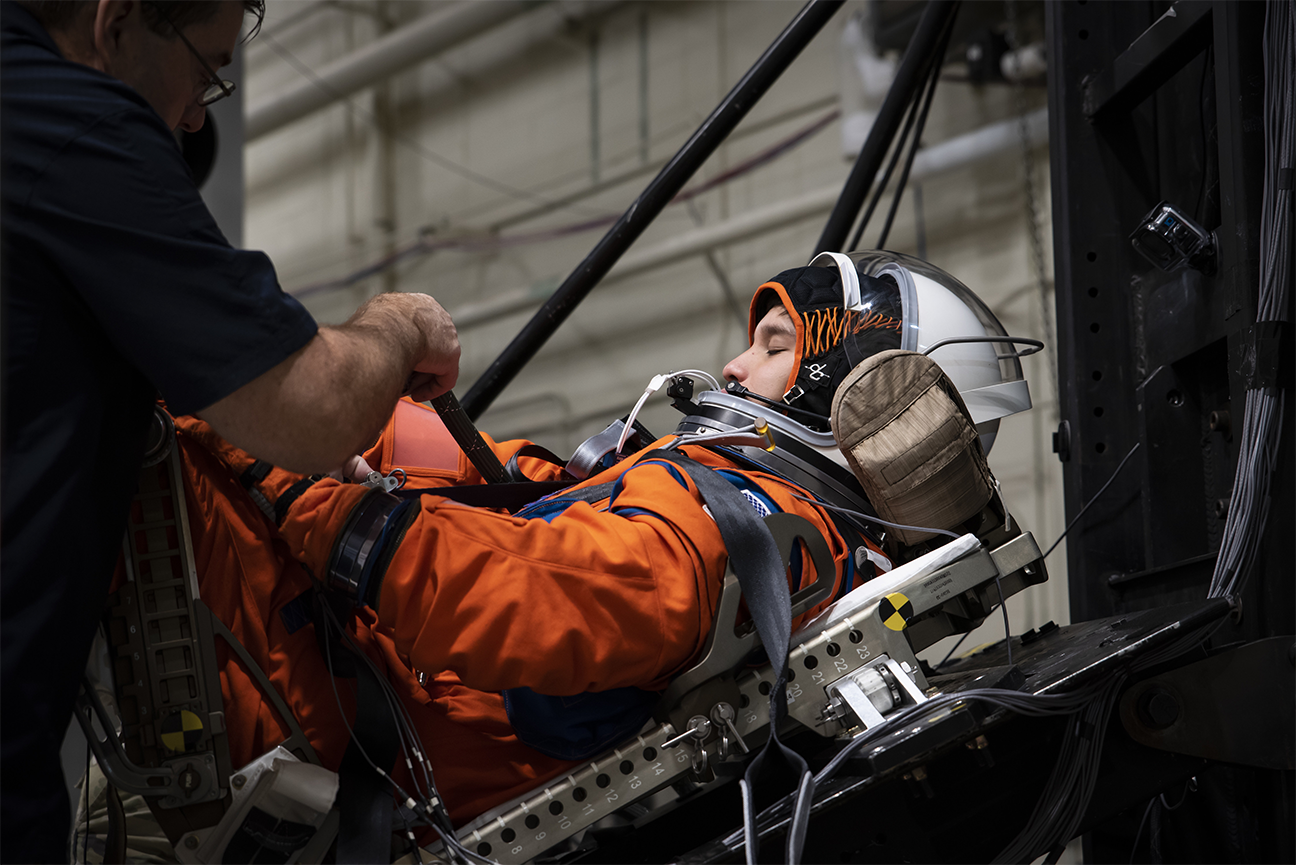
A U.S. Air Force volunteer, who tests the next replica of a flight suit and seat for the Orion space capsule, is strapped into the seat in the drop tower facility at Wright-Patterson Air Force Base, Ohio, Nov. 3, 2023. Researchers with the Air Force Research Laboratory’s Human Effectiveness Directorate tested equipment along with NASA for the Orion space capsule’s upcoming mission to the moon. (U.S. Air Force photo / Richard Eldridge)
Gohmert extended his thanks to the individuals he collaborated with and gained knowledge from over the last 15 years.
“For all the years we’ve been here, just huge thanks to Wright-Patterson for hosting us all these years, and to Chris Perry and all the team, including [teammates who are] no longer with us,” Gohmert said. “It’s a lifetime’s worth of experiences that they’ve given to us, and I don’t think we’re going to ever repay that hospitality. It’s been great.”
For more information about the Artemis II mission, visit https://www.nasa.gov/missions/artemis/nasas-first-flight-with-crew-important-step-on-long-term-return-to-the-moon-missions-to-mars/.
CLICK IMAGE BELOW FOR FULL IMAGE GALLERY

An Air Force Research Laboratory, or AFRL, team works with NASA and a U.S. Air Force volunteer on the horizontal sled test facility at Wright-Patterson Air Force Base, Ohio, Oct. 23, 2023, to test the next replica of a seat and flight suit for the Orion space capsule. Researchers with the AFRL Human Effectiveness Directorate tested equipment for the Orion space capsule’s next mission to the moon. (U.S. Air Force photo / Richard Eldridge)
ABOUT AFRL
The Air Force Research Laboratory is the primary scientific research and development center for the Department of the Air Force. AFRL plays an integral role in leading the discovery, development, and integration of affordable warfighting technologies for our air, space and cyberspace force. With a workforce of more than 12,500 across nine technology areas and 40 other operations across the globe, AFRL provides a diverse portfolio of science and technology ranging from fundamental to advanced research and technology development. For more information, visit www.afresearchlab.com.
ARTEMIS TESTING VIDEO