AFRL Materials Characterization Facility pushes state of the art
WRIGHT-PATTERSON AFB, Ohio (AFRL) – The Air Force Research Laboratory has recently renovated their materials characterization facility (MCF) to meet the ever-advancing needs of materials research. By renovating 3,700 square feet of existing laboratory space, the facility has been designed to keep pace with analytical research technology, thereby “future-proofing” it for the next generation of instrumentation, according to program manager Dr. Todd Butler. A May 26 ribbon-cutting ceremony officially opened the new facility.
“Advanced instrumentation is growing increasingly sensitive to the local environment,” said Butler, “and this requires a strict level of environmental control to ensure the acquisition of high quality data and resolution. This renovation increases our existing capabilities, but also serves to future-proof us as technology exponentially advances.”
Butler went on to describe the challenges of renovating an older building like this. He explained that a lot of the buildings were built many years ago and weren’t necessarily designed for the strict environmental requirements associated with high-resolution electron microscopy.
While the newly renovated lab is housed at the Materials and Manufacturing Directorate, it also serves other technical directorates at Wright-Patterson, as well as university and industrial members who collaborate with the Air Force through a variety of research partnerships.
The larger facility is made up of smaller, environmentally isolated labs. Each of these smaller labs has a suite of instrumentation that draws from a variety of light optical microscopes, an electron probe micro-analyzer, five scanning electron microscopes, three transmission electron microscopes, three dual-beam focused ion beams, a pico-second laser milling system, X-ray powder diffraction and nanoscale X-ray computed tomography. The facility also houses a suite of tools for the simulation and analysis of characterization data.
The new facility also includes fully equipped prep labs for hard or soft materials and cryogenic electron microscopy. “The collection of these capabilities allow users to probe, simulate and analyze a wide range of material and device attributes,” said Butler, “including microstructure, crystallography, chemistry, defects and functional performance.”
All lab spaces within the renovation operate on a dedicated HVAC system ensuring precise temperature and humidity control. To further isolate the instrumentation suites, electromagnetic interference (or “EMI”) from overhead light fixtures, as well as vibration and sound outside the room are all tightly controlled. “All of our lab suites,” said Butler, “have been designed with low EMI fixtures and STC 50 rated doors and windows.” STC, or Sound Transmission Class, is a rating of how well a building’s walls or doors suppress sound. A partition with an STC of 50 will effectively mitigate these disturbances from surrounding areas.
Instrument disturbance is further reduced by the use of remote operator stations, adjacent to the instrument suites. “With some of our highest resolution instruments,” said Butler, “just being in the room and doing things like moving a chair or opening a door can degrade resolution [on a high resolution transmission electron microscope].” As a result, keeping the user isolated from the microscope can be crucially important.
This notion of “remote” operation doesn’t necessarily mean the operator is just outside the room on the other side of the partition. Staff can operate instruments from across AFRL and even from home.
“We are tapped into Ohio’s high speed internet (OARnet) to provide access to the advanced instrumentation across the country,” explained Butler, “from the Ohio State University’s Center for Electron Microscopy and Analysis (CEMAS) to microscopy facilities at other universities and national laboratories. So effectively, we can control the instruments [and see atoms] from anywhere.”
It’s also important to note that the true purpose of the new facility is to support the mission of the warfighter by enabling advanced technology development. “The newly renovated lab will support Air Force science and technology by providing the seamless integration, application and development of advanced materials characterization techniques and expertise,” said Butler.
Acting Materials and Manufacturing Director Dr. Charles Ward stressed the importance of the new lab, even from the perspective of a non-materials scientist.
“There are microscopic features within a material that determine its properties at nearly all levels of scale,” said Ward, “from the atomic scale all the way up to the component level. Understanding how these features form and impact material properties is at the heart of materials science. A cutting-edge characterization facility gives us much improved insight into these features and is essential to developing new materials to deliver warfighter capabilities.”
Dr. Richard Vaia, Chief Scientist at AFRL’s Materials and Manufacturing Directorate, stressed the significance of the new lab in materials development, now and well into the future. “Systems that push the edge of technology are made from materials that push the edge of possibility,” said Vaia. “This was true for the Wrights, and will be the foundation of future air and space system concepts for 2030 and beyond.”
“The magic of materials, and the way that they are made,” continued Vaia, “begins with their structure. Thus, core to the Department of the Air Force’s Materials and Manufacturing Science and Technology enterprise is the ability to measure the structure of these future materials.”
“The MCF lab is the heart of this ability, and the renovation will ensure our scientists, engineers and their partners across U.S. industry and academia have the most advanced techniques to accelerate research and development at the convergence of nanotechnology, biotechnology, quantum science, automation and other emerging scientific fields to invent the stuff that is necessary to build the systems for our future Air Force.”
Although Dr. Butler is the point of contact for the new facility and manages the overall contract, he is also a researcher for the Metals Branch, Structural Materials Division. As such, he is one of the many scientists who will be using the lab.
“It was an exciting opportunity to work collaboratively across the organization to enable the success of this renovation effort,” said Butler, “and I look forward to seeing the enhancement of our materials research spanning metals, ceramics, polymers, semiconductors, composites and biological materials.”
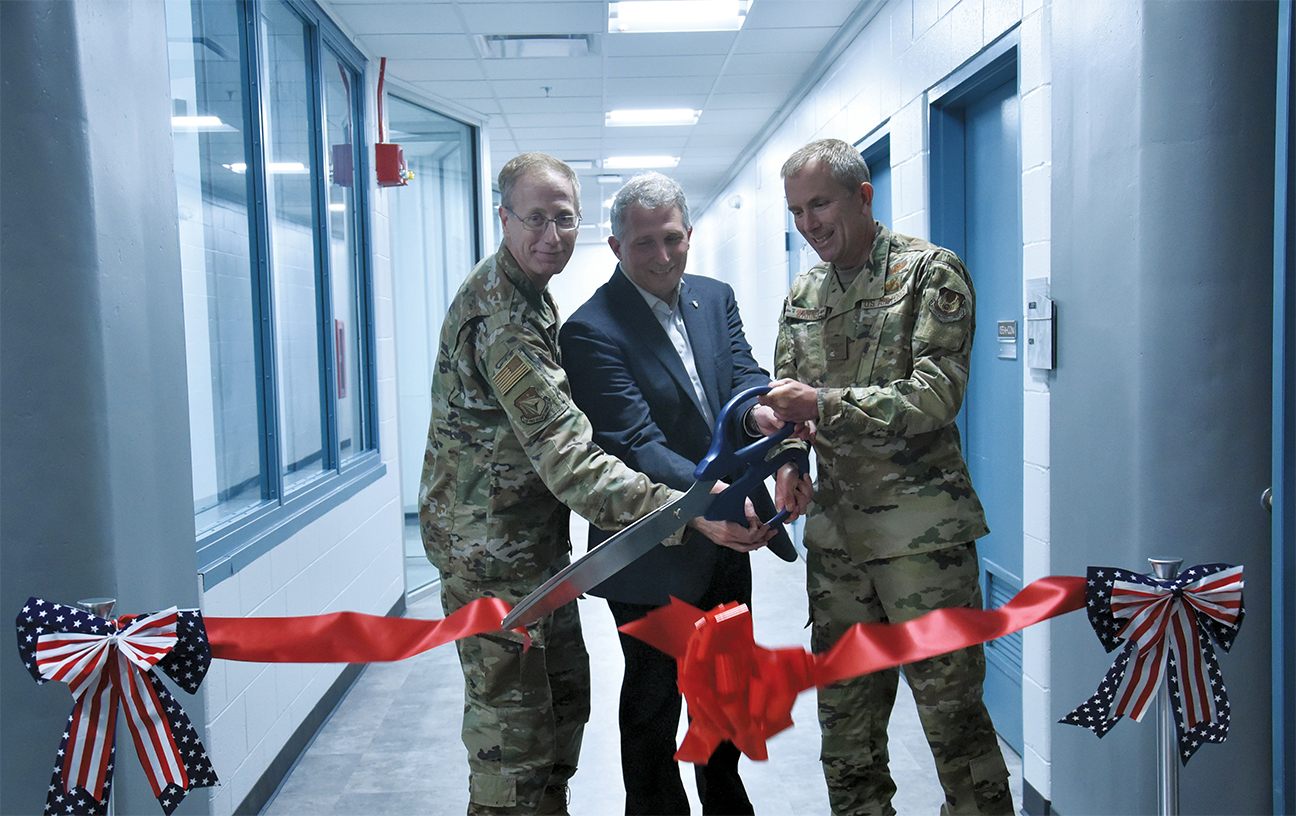
From left to right, AFRL Vice Commander Col. Paul Henderson, Materials and Manufacturing Directorate Chief Scientist Dr. Richard Vaia, and Deputy Director Col. Michael Warner cut the ribbon to open the renovated Materials Characterization Facility at Wright-Patterson Air Force Base. (U.S. Air Force photo/Spencer Deer)