AFRL uses Small Business Innovation Research and Title III programs to deal with supply chain problems
WRIGHT-PATTERSON AIR FORCE BASE, Ohio (AFRL) – Small Business Innovation Research (SBIR) and Defense Production Act (DPA) Title III programs at Wright-Patterson’s Air Force Research Laboratory have recently resulted in a huge success for two American, family-owned businesses: Minnesota Wire and Conductive Composites. An unanticipated additional benefit of this partnership turned out to be a significant repair for a serious medical supply chain weakness.
SBIR programs are highly competitive programs for engaging domestic small businesses in Federal research and development. DPA Title III programs work to ensure domestic industrial resources needed for national defense are readily available. A major goal of both programs is to reduce — or eliminate — America’s reliance on foreign manufacture of materials that are essential to the Department of Defense.
The term “supply chain disruption” is new to many people these days. However, Minnesota Wire, a 55-year-old family business, was already seeing supply chain disruptions even before the COVID-19 pandemic. This was especially so from their Asian suppliers. Domestic suppliers of critical materials that were needed for making wire sets — for example, copper — were few to nonexistent. However, customers for the wire sets, mainly in the medical field (for example, hospitals and emergency services), simply could not wait. Of course, demand got exponentially worse in early 2020 with the onset of the pandemic. Reliance on domestic manufacturing suddenly became more important than ever. A domestic supply of raw materials was far less likely to be disrupted and could also handle the unexpected increase in demand brought on by emergencies like the COVID-19 pandemic.
This is where Conductive Composites came to play a critical role.
A family-owned business that began in 1984, Conductive Composites had already developed a method for coating carbon-fiber wires with nickel. The result was a wire that was translucent to X-rays — a product that had many applications in medicine. Thus, for most medical uses, nickel-coated carbon wire was better than copper wire.
According to Nate Hansen, CEO of Conductive Composites, when his company competed for and won a SBIR contract in 2010 with AFRL’s Materials and Manufacturing Directorate, the Air Force had an interest in nickel-coated carbon fiber for a number of different applications.
Unfortunately, although Conductive Composites still had the expertise, they no longer had the actual capability. Hansen explained that his company had already decided to focus on other parts of the business a few years earlier. “We had sold the nickel-plated fibers part of the business to International Nickel. They moved all of the coating processes over to Europe, and eventually decided they couldn’t make that product anymore in about 2004.” According to Hansen, “It didn’t take long for some big gaps in the market to open up. So we began re-shoring and modernizing our production capability for it.”
One such market facing those gaps was the Air Force. According to Max Alexander, Principal Materials Engineer for the Air Force Research Laboratory, “Conductive would not have even begun coating fiber domestically again if not for the support of Air Force SBIR and DPA Title III investments.”
Alexander went on to stress the importance to the DoD of having a reliable commercial manufacturer of critical materials here in the USA. However, the value of a domestic source for wiring goes far beyond national defense. Supply chain problems have also affected manufacturers of specialty wiring used by the medical sector.
Although Minnesota Wire still uses copper for many applications, they mostly use carbon-fiber conductor from Conductive Composites to make medical wiring. They create the finished product by covering nickel coated carbon fiber from Conductive Composites with plastic insulation, cutting it to proper lengths for wiring sets, and installing connectors on the ends of the wires. In the past decade, Minnesota Wire has fielded 7 million medical wire sets that use material from Conductive Composites. This is equivalent to over 3500 miles of wire.
Minnesota Wire has seen a steady growth in orders as they continue to prove out their position as the preferred provider of medical wiring. However, things got difficult once the pandemic arrived, creating an increased demand accompanied by a skyrocketing supply chain disruption.
Minnesota Wire was already using metal-coated carbon fiber from Conductive Composites for a significant portion of their products. So to offset their foreign supply chain problems — in particular those associated with buying copper — they have been transitioning to using carbon fiber for an even larger portion of their product.
“Current conditions have pushed our company output to focus almost entirely on medical products,” said Paul J. Wagner, the CEO of Minnesota Wire. “Fiber from Conductive Composites is needed for half of that production, and their ability to deliver critical materials is more important than ever right now to keep production going for the medical industry.”
Alexander has nothing but praise for the effectiveness of the SBIR and DPA Title III programs and the two companies that benefitted from them. “The valuable seeds that were planted by these programs continue to yield a high-return harvest,” he said. “Both Minnesota Wire and Conductive Composites look forward to continuing to keep the domestic supply chain strong and will assist in any way possible.”
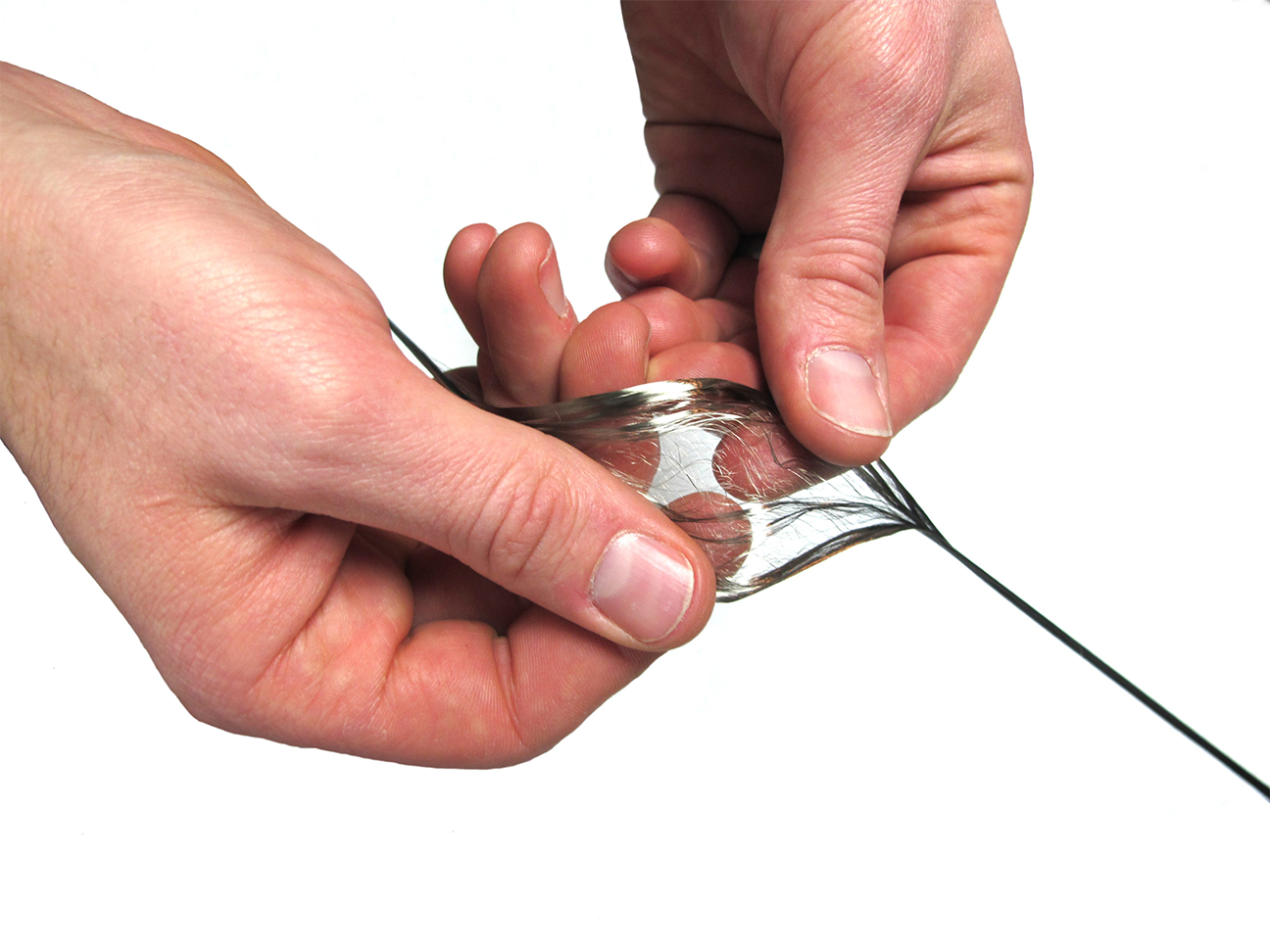
An X-ray translucent wire, shown here, is made of strands of nickel-plated carbon fibers. (Courtesy photo/Minnesota Wire)