Take the load off: Exoskeleton to enhance safety, retention for aerial porters, others
WRIGHT-PATTERSON AIR FORCE BASE, Ohio (AFRL) — Aerial porters are responsible for the management and movement of passengers and cargo transported through airlift. And the cargo these aerial porter teams load and unload can range from large pallets of equipment, gear and food to Unmanned Aerial Vehicles, High Mobility Artillery Rocket System trucks, Abrams tanks and more.
So imagine not just the individual strength and conditioning required of each porter to move weight of this magnitude, but also the number of porters required for various missions. It usually takes multiple people pushing and pulling, loading and unloading this massive cargo into the back of cargo aircraft.
Needless to say, the aerial porter career field sees its share of injuries — acute as well as long-term — that can sometimes force them out of the career field and sometimes even out of the service. But relief could be on the horizon.
The Air Force Research Laboratory’s Center for Rapid Innovation, or CRI, held an event Oct. 6, 2022, with host organization, the Air Force Reserve Command’s 445th Airlift Wing, for a team from ROAM Robotics to demonstrate the latest iteration of their FORGE System, a pneumatically-powered exoskeleton that Airmen and Guardians can wear that has the ability to augment leg strength in order to reduce fatigue, increase endurance and offset weight. Think – Iron Man but without Marvel and its fictive spin. Think – real-world applications for the military.
The event began with a presentation of the pneumatically-powered exoskeleton system, which is supported by Direct to Phase II Small Business Innovation Research project called Radical Improvements in Personnel Performance through Enhanced Development, or RIPPED. Then, participants were escorted to an aircraft hangar. Two aerial porters from the 87th Aerial Port Squadron, part of the 445 AW, waited in the back of a C-17 to demonstrate the technology.
The two aerial porters, Chief Master Sgt. Sean Storms, 87th APS aerial port manager, and Senior Master Sgt. Brian Anders, 87th APS assistant aerial port manager, donned the technology, which consisted of actuated leg braces and a backpack, and moved a pallet that weighed about 3,500 pounds. The porters said moving something that heavy would typically take four to five people, but with the exoskeleton system, the two men moved the pallet on their own.
“I can definitely tell a difference; there’s a lot less pressure on my knees and I can feel the assist this system gives,” said Storms.
Following the demo, participants were invited to try out the exoskeleton with assistance by the ROAM Robotics team. Some put it on and climbed a set of stairs in the hangar while carrying weights. Others tested it by pushing a weighted sled across the grass outside or doing squats in the squadron gym. Regardless of the test, participants could hear the exoskeleton’s air bladder actuators engaging as they moved. Life seemed to be imitating art during the demonstration.
John Florio, deputy director of CRI, explained that this technology could be a game changer for the aerial port community.
“If this is optimized for the aerial porters’ particular missions, it is going to mean that teams will be able to load heavier objects on aircraft much faster using less people, which equates to saving the government and taxpayer money,” he said. “But the biggest game changer for the Air and Space Forces is less injuries to personnel, which can lead to longer careers.”
Florio explained the weight the aerial porters are required to move during missions, sometimes in austere environments or under fire is unlike what some may experience when moving to a new home or office.
“If you’ve ever loaded anything in an office or maybe at home like a refrigerator — anything like that is small compared to what our aerial porters are loading. For them, we’re talking about large pieces of cargo going into a large aircraft,” he said. “So knees are under stress — ankles are under stress — backs are under stress — muscles all over the body are under stress. I’ve talked to a lot of the people here in the maintenance squadron, and chronic injuries are rampant all over this particular career field and in other related fields, too.”
Some of those “other related fields” that Florio mentioned were on the mind of Brig. Gen. John Andrus, the 711th Human Performance Wing commander in AFRL, who also attended the demonstration.
“I can see additional uses for this pneumatically-powered exoskeleton, primarily in aeromedical evacuation missions where our medical personnel are lifting large litters of sick and injured warfighters into the back of aircraft,” Andrus said. “We have to think about the safety of our medical personnel, but also the safety of those we are treating and evacuating out of harm’s way.”
Participants asked about other potential career fields that might benefit from the assisted technology. Tim Swift, ROAM Robotics CEO, stated that the system could be adapted to fit other missions, but for now, attention was on providing relief to the aerial porter community, which he said sees an estimated $31 million in annual disability benefits and suffers from lost workday injuries.
“The opportunity to have something like this exoskeleton, that provides a capability that augments the aerial porter’s strength, that takes pressure off joints, that makes their muscles work more efficiently, and in the long run, that prevents overuse injuries – well,” said Florio, “it’s going to be a game changer.”
AFRL established its Center for Rapid Innovation to streamline the application of new and existing technologies that address dynamic changes in air, space, ground and cyber battlespaces and solve evolving and urgent operational challenges. The unique process employs diverse subject matter expertise and a collaborative government-industry technical and management capability to rapidly develop, test and deploy innovative prototype solutions for dynamic operational environments. The Ultra LEAP unmanned air platform, which completed its initial successful flight tests in 2019, is another example of technology developed by CRI.
About AFRL
The Air Force Research Laboratory, or AFRL, is the primary scientific research and development center for the Department of the Air Force. AFRL plays an integral role in leading the discovery, development, and integration of affordable warfighting technologies for our air, space and cyberspace force. With a workforce of more than 11,500 across nine technology areas and 40 other operations across the globe, AFRL provides a diverse portfolio of science and technology ranging from fundamental to advanced research and technology development. For more information, visit: www.afresearchlab.com.
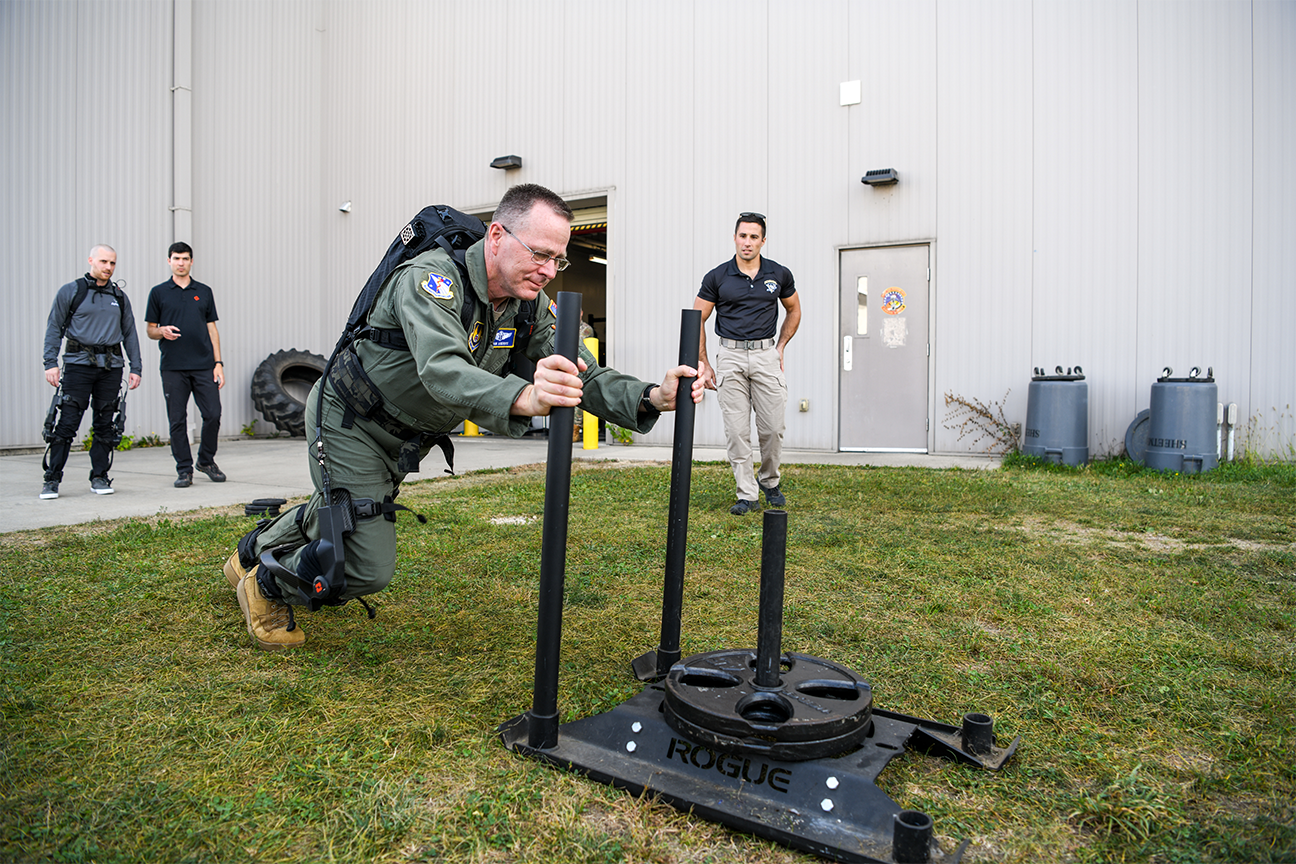
Brig. Gen. John Andrus, commander of 711th Human Performance Wing in the Air Force Research Laboratory, pushes a weighted sled while wearing the pneumatically-powered exoskeleton during an AFRL demonstration Oct. 6, 2022, at the Air Force Reserve Command’s 445th Airlift Wing, Wright-Patterson Air Force Base, Ohio. This technology, supported by AFRL’s Center for Rapid Innovation, was designed to assist aerial porters load and unload heavy cargo and is intended to minimize manpower needed as well as prevent injuries. (U.S. Air Force photo / Patrick O’Reilly)
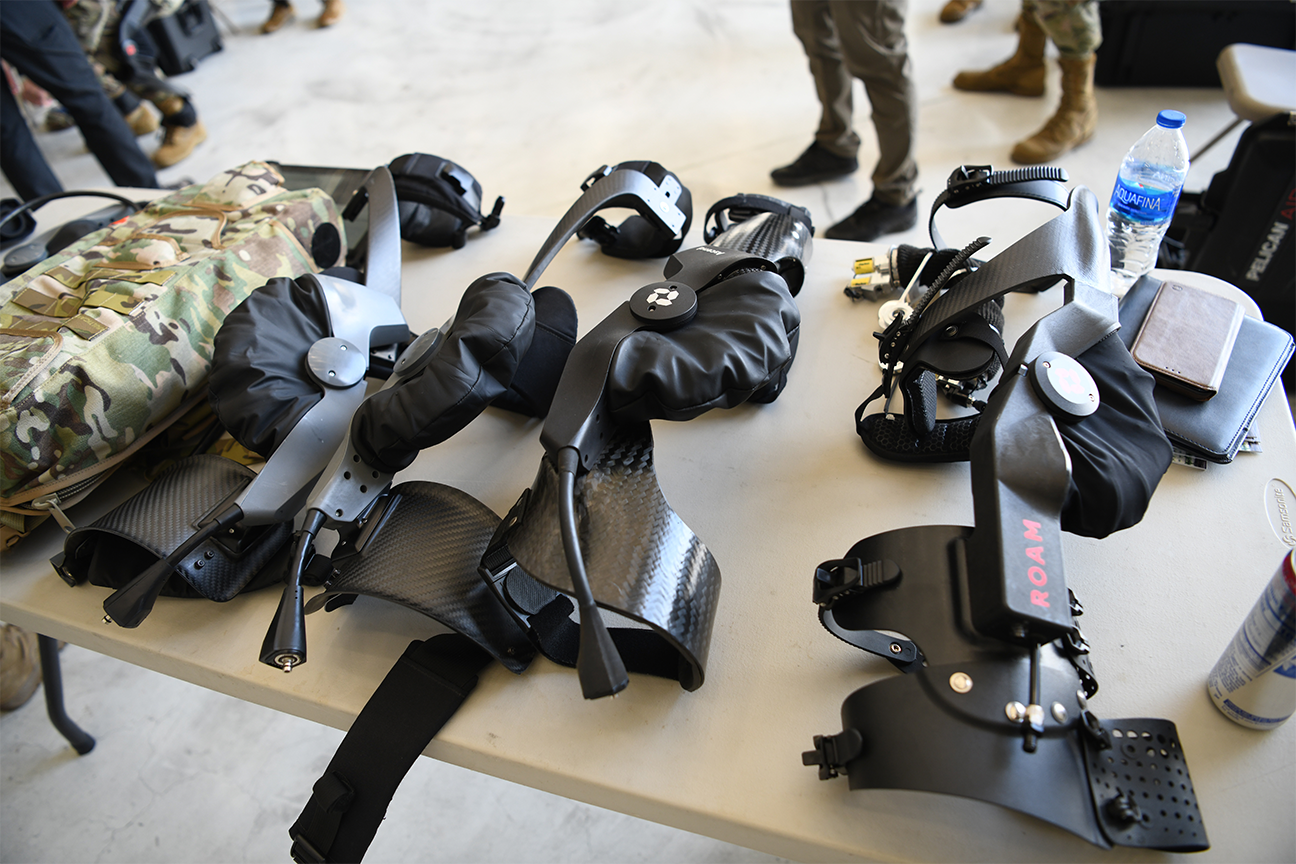
The pneumatically-powered exoskeleton, developed by ROAM Robotics as part of a Direct to Phase II Small Business Innovation Research grant, is displayed during an Air Force Research Laboratory demonstration Oct. 6, 2022, at the Air Force Reserve Command’s 445th Airlift Wing, Wright-Patterson Air Force Base, Ohio. This technology, supported by AFRL’s Center for Rapid Innovation, was designed to assist aerial porters load and unload heavy cargo and is intended to minimize manpower needed as well as prevent injuries. (U.S. Air Force photo / Patrick O’Reilly)
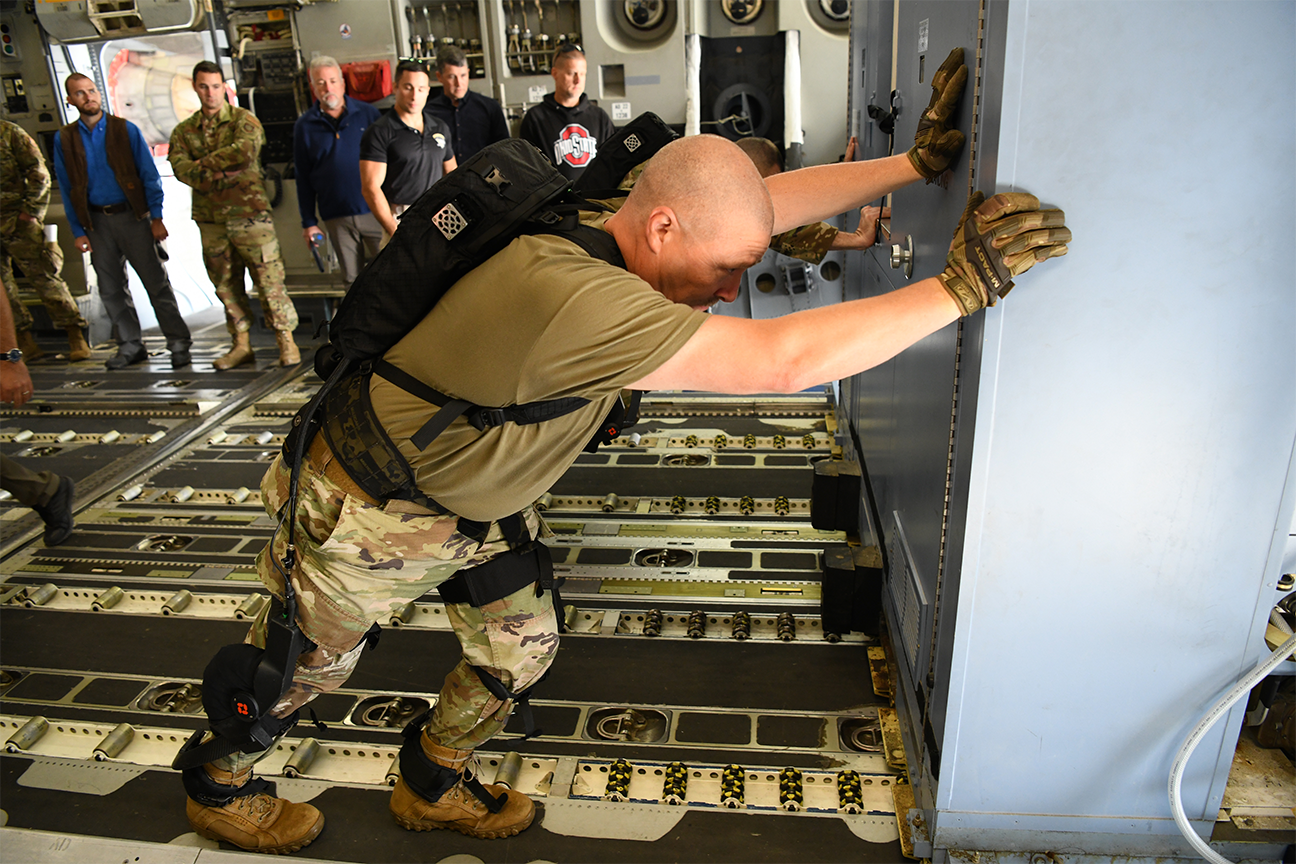
Chief Master Sgt. Sean Storms, aerial port manager with the Air Force Reserve Command’s 445th Airlift Wing, Wright-Patterson Air Force Base, Ohio pushes oversized cargo across the floor of a C-17 Oct. 6, 2022, during an Air Force Research Laboratory demonstration of a pneumatically-powered exoskeleton system developed by ROAM Robotics. This technology, supported by AFRL’s Center for Rapid Innovation, was designed to assist aerial porters load and unload heavy cargo and is intended to minimize manpower needed as well as prevent injuries. (U.S. Air Force photo / Patrick O’Reilly)
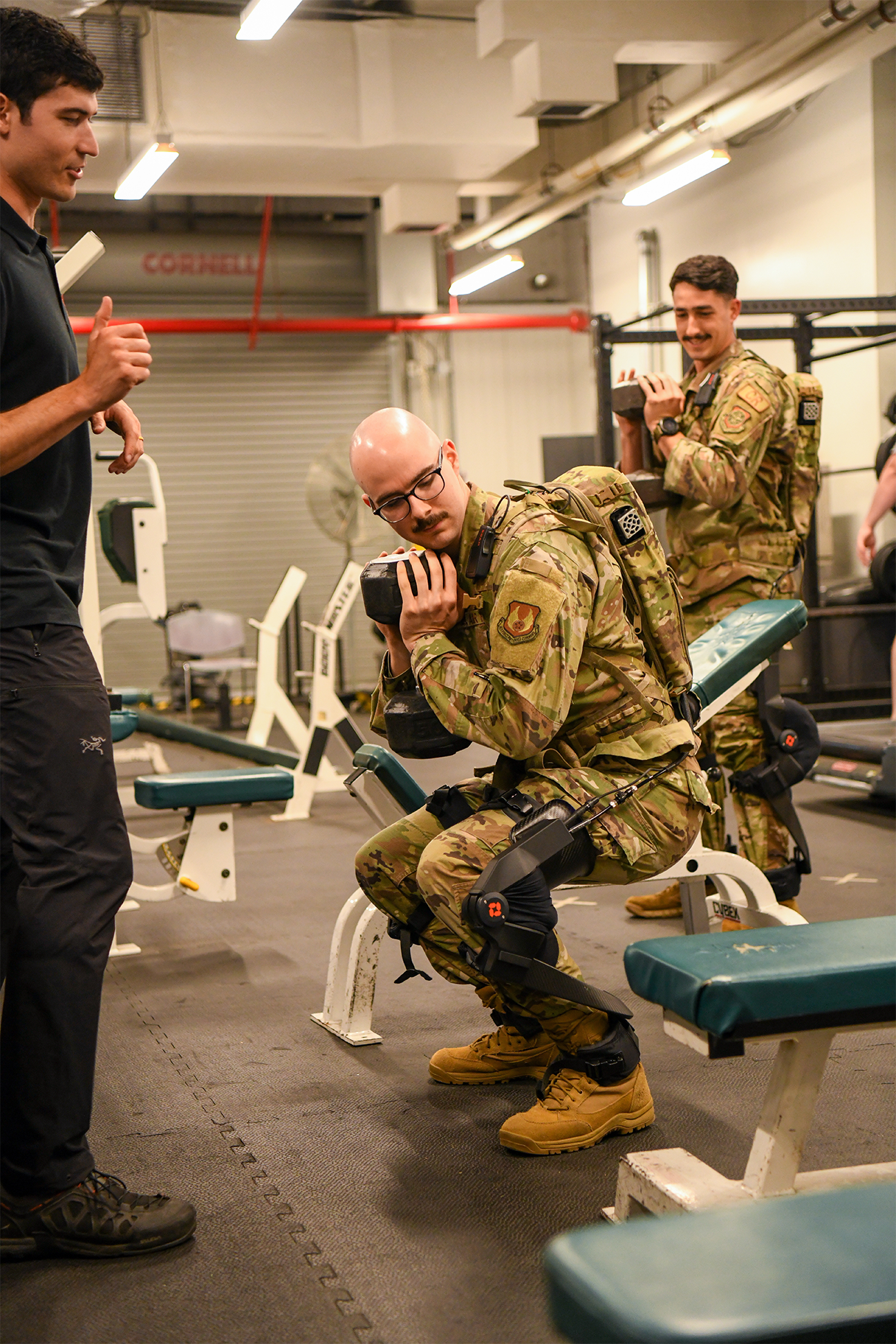
2nd Lt. Ian Casciola, special warfare electrical engineer with the 711th Human Performance Wing in AFRL, performs a squat while wearing a pneumatically-powered exoskeleton system, developed by ROAM Robotics, during an AFRL demonstration Oct. 6, 2022, at the 445th Airlift Wing, Wright-Patterson Air Force Base, Ohio. This technology, supported by AFRL’s Center for Rapid Innovation, was designed to assist aerial porters load and unload heavy cargo and is intended to minimize manpower needed as well as prevent injuries. (U.S. Air Force photo / Patrick O’Reilly)
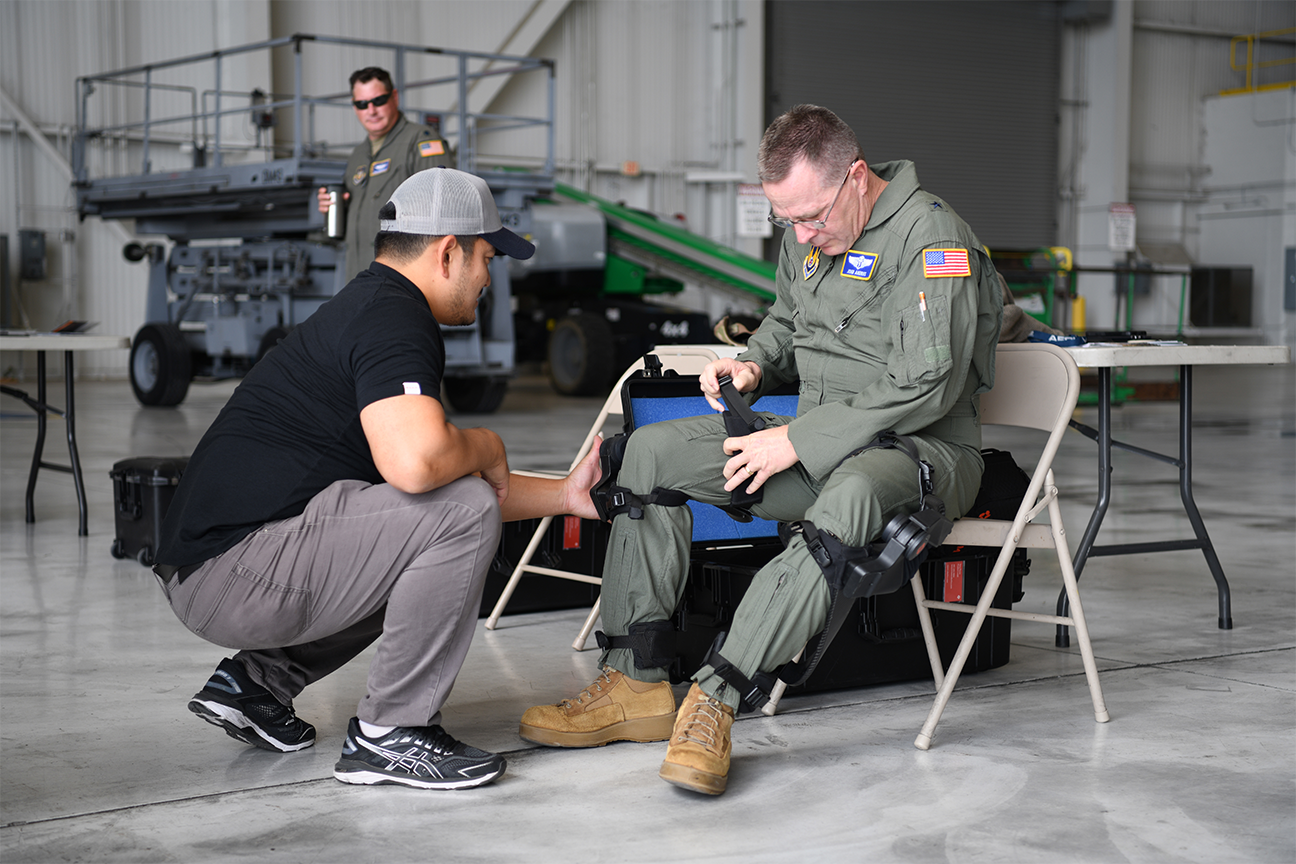
Brig. Gen. John Andrus, commander of 711th Human Performance Wing in the Air Force Research Laboratory, dons the pneumatically-powered exoskeleton with assistance from Dr. Linus Park with ROAM Robotics during an AFRL demonstration Oct. 6, 2022, at the 445th Airlift Wing, Wright-Patterson Air Force Base, Ohio. This technology, supported by AFRL’s Center for Rapid Innovation, was designed to assist aerial porters load and unload heavy cargo and is intended to minimize manpower needed as well as prevent injuries. (U.S. Air Force photo / Patrick O’Reilly)