AFRL demonstrates new augmented reality capability to improve DAF nondestructive inspections
WRIGHT-PATTERSON AIR FORCE BASE (AFRL) — The Air Force Research Laboratory, or AFRL, has developed an augmented reality capability to assist in accomplishing nondestructive inspections, or NDI, for safety critical applications in military aircraft. Research engineers in AFRL’s Materials and Manufacturing Directorate designed the Augmented Reality for Nondestructive Evaluation, or ARNE, system to help aircraft technicians detect fatigue cracks between metal aircraft layers using a bolt hole eddy current, or BHEC, procedure, contributing to airworthiness and improved fleet readiness for the U.S. Department of the Air Force.
“ARNE meets a crucial need for nondestructive inspection methods by providing hands-on refresher coaching for our NDI technicians out in the field,” said 1st Lt. Svanna Perseghetti, nondestructive research engineer, AFRL’s Materials and Manufacturing Directorate. “Our aircraft maintainers and technicians are already fully trained and fully certified, but everyone benefits when they have access to review opportunities to ensure that they can practically apply what they learn.”
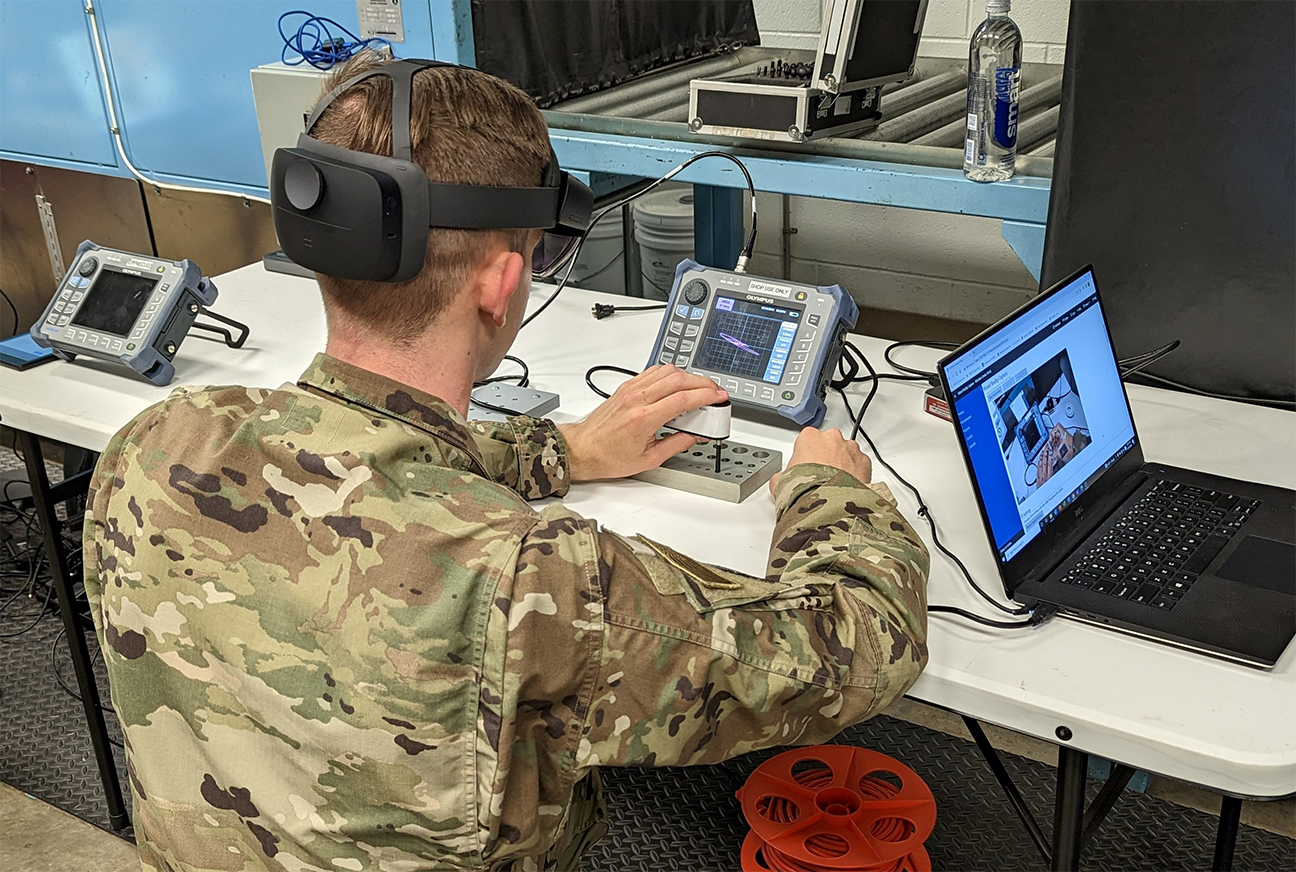
A senior Airman from the U.S. Air Force’s 19th Maintenance Group tests the Augmented Reality for Nondestructive Evaluation, or ARNE, system using a bolt hole eddy current, or BHEC, inspection review module at Little Rock Air Force Base, Arkansas, in December 2022. BHEC inspection is used for safety critical structural applications when other methods do not meet capability requirements, said Dr. Eric Lindgren, nondestructive technology lead, Materials and Manufacturing Directorate. As the procedure requires removal of fasteners, it is the method of “last resort” to address safety critical applications, and as such is not frequently performed by many U.S. Air Force NDI technicians. ARNE provides airmen the opportunity to review BHEC inspection procedures virtually to increase confidence. (U.S. Air Force photo)
ARNE utilizes augmented reality, or AR, a technology that superimposes a computer-generated image onto a user’s view of the real world. The system projects relevant three-dimensional hologram images onto physical aircraft parts and virtually “walks” technicians through the process of performing a BHEC procedure, a critical aircraft safety inspection used to detect the presence of fatigue cracks in DAF fleets, said Dr. Eric Lindgren, nondestructive technology lead, AFRL’s Materials and Manufacturing Directorate.
“We asked ourselves: how can we give Airmen some kind of tool that they can use to re-familiarize themselves with what they already know?” Lindgren said. “The arrival of augmented reality offers a great capability, because now we have access to what is essentially an interactive refresher. Video tutorials can be helpful, but imagine if that same video is overlaid precisely on a component they are inspecting? ARNE walks them through a series of processes by superimposing actual equipment and the interfaces that they see, in their direct field of use, so the information is right in front of them.”
The end result is increased confidence to accomplish standard inspections as intended, Lindgren said.
Typically, aircraft maintenance technicians learn how to perform safety inspections using traditional 2D-methods of instruction, such as written manuals and presentation slides, Perseghetti said, and they do not gain extensive hands-on, tangible aircraft inspection experience until they are deployed to an air base or depot.
Fatigue cracks can occur over the lifecycle of metal airframe, especially when their life is extended beyond the original design life, Lindgren said. Over time fatigue cracks can nucleate and grow, which impacts aircraft integrity, or safety, and availability if not detected early before they grow to and beyond critical size.
“Cracks occur when stresses are localized, and stresses are highly concentrated at faying surfaces — between the metal layers held together by fasteners,” Lindgren said. “Repetitive elastic loads that do not cause permanent deformation cause metal fatigue in aircraft. Much like a wire, if you bend it enough times, tens of thousands for elastic loads, it becomes hard to bend. Eventually this location can be the site of crack nucleation and growth, leading to failure.”
BHEC inspection is used for safety critical structural applications when other methods do not meet capability requirements, Lindgren added. As the procedure requires removal of fasteners, it is the method of “last resort” to address safety critical applications, and as such is not frequently performed by many U.S. Air Force NDI technicians.
“As we depend on reproducible capability to ensure the integrity of our systems, it is critical that Airmen can accomplish this inspection correctly,” Lindgren said. “In addition, confidence in performance results in less rework and increases aircraft availability. We need to have every Airman, no matter what they’re inspecting, have the same capability to detect flaws.”
So far, Perseghetti said, ARNE has been successfully demonstrated at Little Rock Air Force Base, Arkansas; Tinker Air Force Base in Oklahoma City, Oklahoma; and at a U.S. Air Force-wide NDI Working Group conference for nondestructive inspectors in Dayton, Ohio. In summer 2022, over 100 Airmen attended the conference, hailing from almost every U.S. depot and air base, and included multiple NDI inspectors from Japan, Korea and other nations, Perseghetti said.
“At these demonstrations, we break out sample aircraft parts, and the technicians go through the ARNE review modules, and they can confirm right there that, yes, they are doing exactly what they are supposed to, this is accurate information, this is a test subject they are familiar with,” Perseghetti said. “As a natural consequence, they gain confidence. I remember meeting an aircraft technician at one of our demos — she put the ARNE headset on, and she was just blown away. She said it was like everything finally clicked.”
Inspiration for the project initially grew from a desire to provide aircraft technicians and maintainers with more modern tools and better technology to help them do their jobs, said Sean Coghlan, chief of Systems Engineering for Air Force Materiel Command Logistics. Coghlan played a crucial role in securing funding for nascent efforts to kick-start and develop ARNE in 2018 while serving as a branch chief in the Materials and Manufacturing Directorate.
“ARNE really speaks to the decidedly more human piece of this challenge,” Coghlan said. “Being able to put modern technology into the hands of these men and women, instead of just handing them a notebook, a pen and a flashlight — it’s a way to recruit and retain the best people, to help keep them refreshed, and to provide them with the tools they need to do their jobs more efficiently and effectively. This is as much about the people and culture within our maintenance community as it is about the technology and enhancing our abilities to detect cracks. It’s very much a people-centered solution.”
ARNE also offers a sneak peek into how the DAF will likely approach operations and maintenance in the not-so-distant future, Coghlan added.
“Our multi-capable Airmen and Guardians of the future are going to have to be skilled and trained in multiple areas of expertise,” Coghlan said. “As they are deployed to more remote and austere locations, they might not always have access to a full complement of staff to provide readiness support. Capabilities [like ARNE] will allow them to tap into a deep knowledge base and enable them to do their jobs at any location, with just a small handful of people. It enhances our ability to equip and train multi-capable Airmen to tackle challenges in the agile combat deployment environment.”
Systems Engineer Capt. Joshua Lynch, currently based at Buckley Space Force Base, Colorado, oversaw development of the ARNE program when efforts initially kicked off in 2018 as a deputy branch chief and program manager in the Materials and Manufacturing Directorate. The program illustrates AFRL’s ability to leverage commercial off-the-shelf products in emerging technology areas, integrate custom software packages and deliver solutions to Airmen on a meaningful and relevant timeline, Lynch said.
“This program was designed completely around the needs of U.S. Department of the Air Force nondestructive inspection technicians and was largely driven by feedback from our Airmen in the field,” Lynch said. “I believe this program will be a pathfinder for AFRL and the greater Air Force when it comes to integrating augmented and mixed reality into the flight line. I am grateful I was able to be part of early efforts to get this project off the ground.”
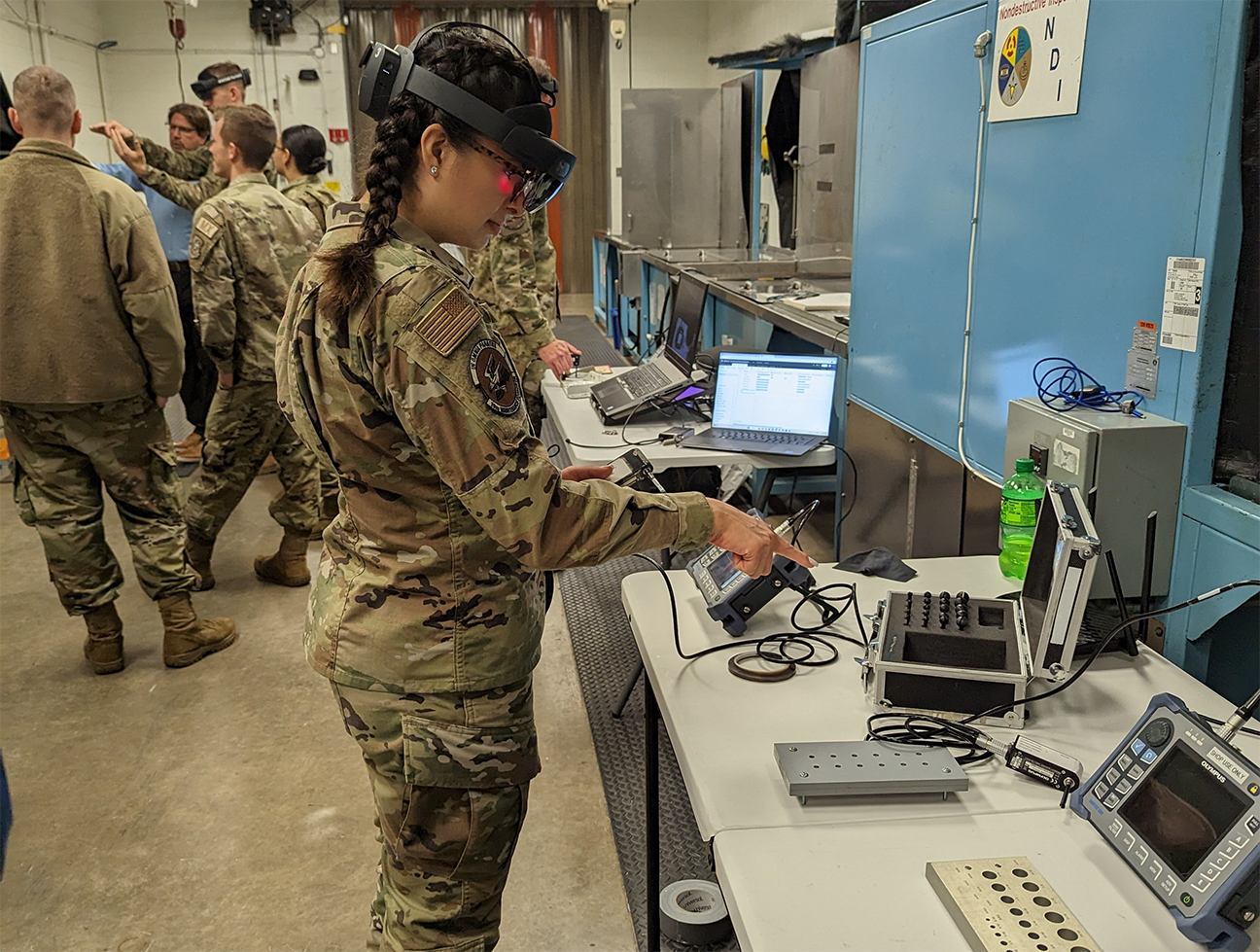
An Airman from the U.S. Air Force’s 19th Maintenance Group prepares to perform a virtual bolt hole eddy current inspection using the Augmented Reality for Nondestructive Evaluation, or ARNE, system at Little Rock Air Force Base, Arkansas, in December 2022. ARNE utilizes augmented reality, or AR, a technology that superimposes a computer-generated image onto a user’s view of the real world. The system projects relevant three-dimensional hologram images onto physical aircraft parts and virtually “walks” technicians through the process of performing a BHEC procedure, a critical aircraft safety inspection used to detect the presence of fatigue cracks in DAF fleets. (U.S. Air Force photo)
About AFRL
The Air Force Research Laboratory is the primary scientific research and development center for the Department of the Air Force. AFRL plays an integral role in leading the discovery, development and integration of affordable warfighting technologies for our air, space and cyberspace force. With a workforce of more than 11,500 across nine technology areas and 40 other operations across the globe, AFRL provides a diverse portfolio of science and technology ranging from fundamental to advanced research and technology development. For more information, visit www.afresearchlab.com.