AFRL enhances Computed Tomography Lab with state-of-the-art infrastructure, imaging capabilities
WRIGHT-PATTERSON AIR FORCE BASE, Ohio (AFRL) — The Air Force Research Laboratory, or AFRL, hosted an official tour of its recently renovated Computed Tomography Laboratory Nov. 9, 2022.
The lab, part of AFRL’s Materials and Manufacturing Directorate, supports nondestructive testing of 3D-printed materials for the Department of Defense’s internal and external customer base.
The Accelerated Materials and Processing Solutions branch arranged the tour to highlight an extensive makeover of its facility, which included the installation of an additional computed tomography, or CT, machine and the construction of a brand-new suite to safely house the added equipment. CT refers to a form of computerized X-ray imaging that can be used to look for potential defects in aerospace-grade materials to ensure airworthiness and durability.
“The lab tour specifically highlighted how [materials and processing] lessons learned and the new Computed Tomography Lab are being applied to safely accelerate implementation of additive manufacturing technologies into emerging and future weapons systems,” said Jeff Stricker, branch chief, Accelerated Materials and Processing Solutions.
The directorate also hosted a formal ribbon-cutting event in the Additive Manufacturing Laboratory to laud the recent completion of major infrastructural improvements within both facilities under a shared funding source.
AFRL Commander Maj. Gen. Heather Pringle, AFRL Executive Director Timothy Sakulich and Materials and Manufacturing Directorate Director Darrell K. Phillipson attended both events.
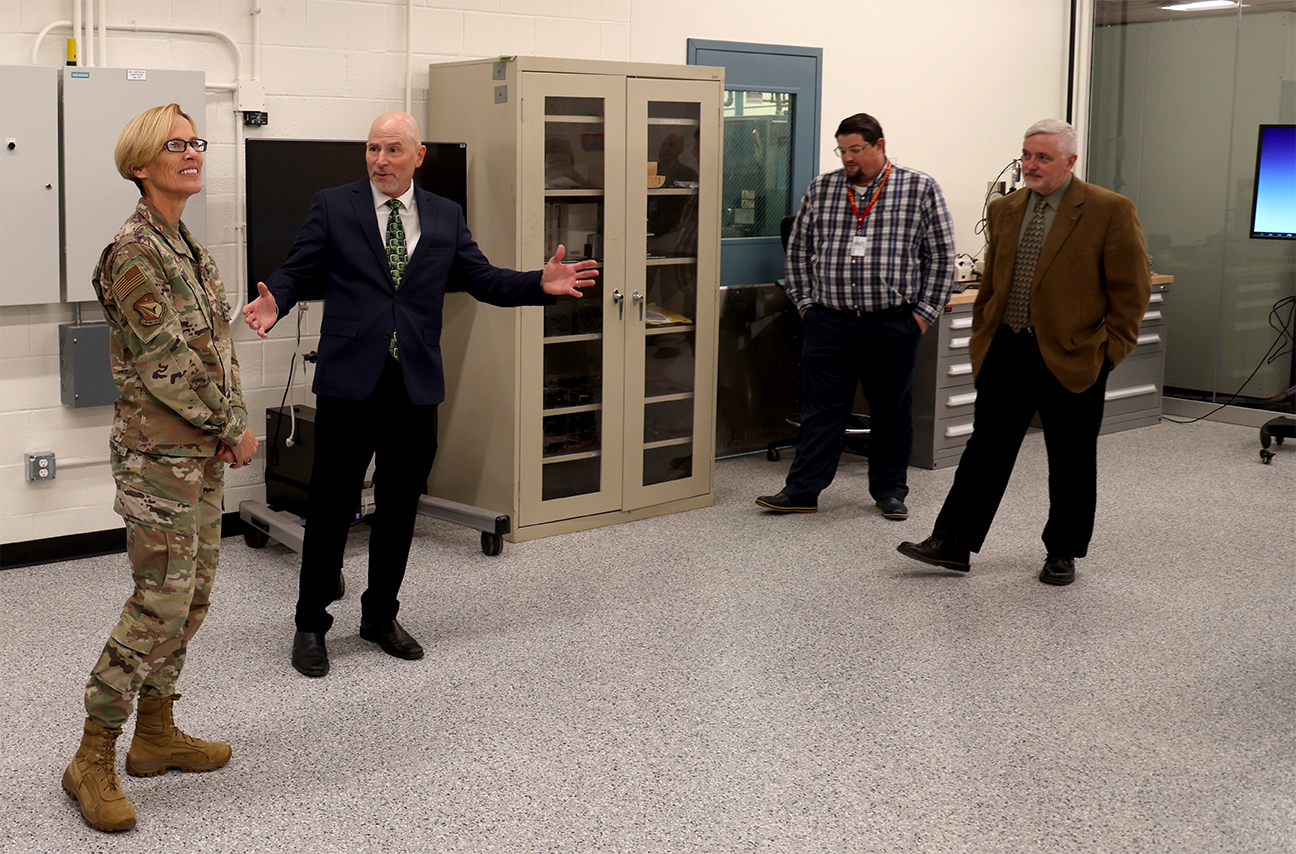
Air Force Research Laboratory, or AFRL, Commander Maj. Gen. Heather Pringle, left, surveys the newly-renovated Computed Tomography Laboratory, Nov. 9, 2022, at Wright-Patterson Air Force Base, Ohio, while John Brausch, center, Ryan Mooers and Steve Thompson, far right, welcome Pringle to the facility. The lab, part of AFRL’s Materials and Manufacturing Directorate, supports non-destructive testing of 3D-printed materials for the Department of Defense’s internal and external customer base. (U.S. Air Force photo / Jonathan Taulbee)
At an informal reception following the tour, Pringle congratulated employees on working together to bring new technological capabilities to the Directorate.
“I can tell that you all have a strong working relationship, and that you are there for each other,” Pringle said. “You are a family.”
Senior Materials Engineer Steve Thompson from the Structural Materials Evaluation section oversaw the project from its inception in conjunction with Matthew Geis, a project engineer from the Engineering Services and Support branch.
“We’re proud to bring this facility into the 21st century,” said Thompson. “These changes will allow us to do our jobs better, and more efficiently.”
The roughly $4.5 million, 6,600-square-foot-facility renovation project was covered by Flex-4 funding and is slated to complete fully by Dec. 2. The Department of Defense provides Flex-4 funds to enable unique research capabilities within its laboratories. Roughly $1 million in supplemental AFRL funding financed the additional computed tomography machine.
“If you’ve ever gone to the doctor and gotten a CT scan to look for a possible broken bone—that’s essentially what this machine does,” Thompson said. “It looks for any potential defects in the quality of the material.”
John Brausch, AFRL technical lead specializing in rapid materials and processes characterization technology, said, “Computed tomography provides a high-resolution 3D reconstruction of X-ray image data to detect and quantify internal geometry, defects, manufacturing errors and failure modes. The technology is crucial for evaluating the quality and integrity of materials with the goal to help accelerate technology solutions to the warfighter.”
Originally, the CT facility possessed only one machine, but the second unit “adds a number of new capabilities. It allows us to inspect larger and denser parts and adds different scanning options to produce higher-quality results,” said Ryan Mooers, a non-destructive evaluation engineer who designed the new CT suite.
AFRL opted to build the new CT room for the additional machine inside of a preexisting space.
“We want to protect our two high-cost pieces of equipment in a climate-controlled environment,” Thompson said. “The new suite has its own heating system, its own cooling system.”
The existing laboratory space remained 85% to 90% functional and operational throughout construction.
Mooers added, “By building the suite, we can ensure that both machines are in the same location and provide us a common location to bring parts. The suite also provides protection and environmental control for the units, keeping [noise] enclosed.”
An added benefit of the suite —as well as cost savings to the Air Force— is that less manpower is needed: a controller can operate the two machines simultaneously, as they are now situated in close proximity.
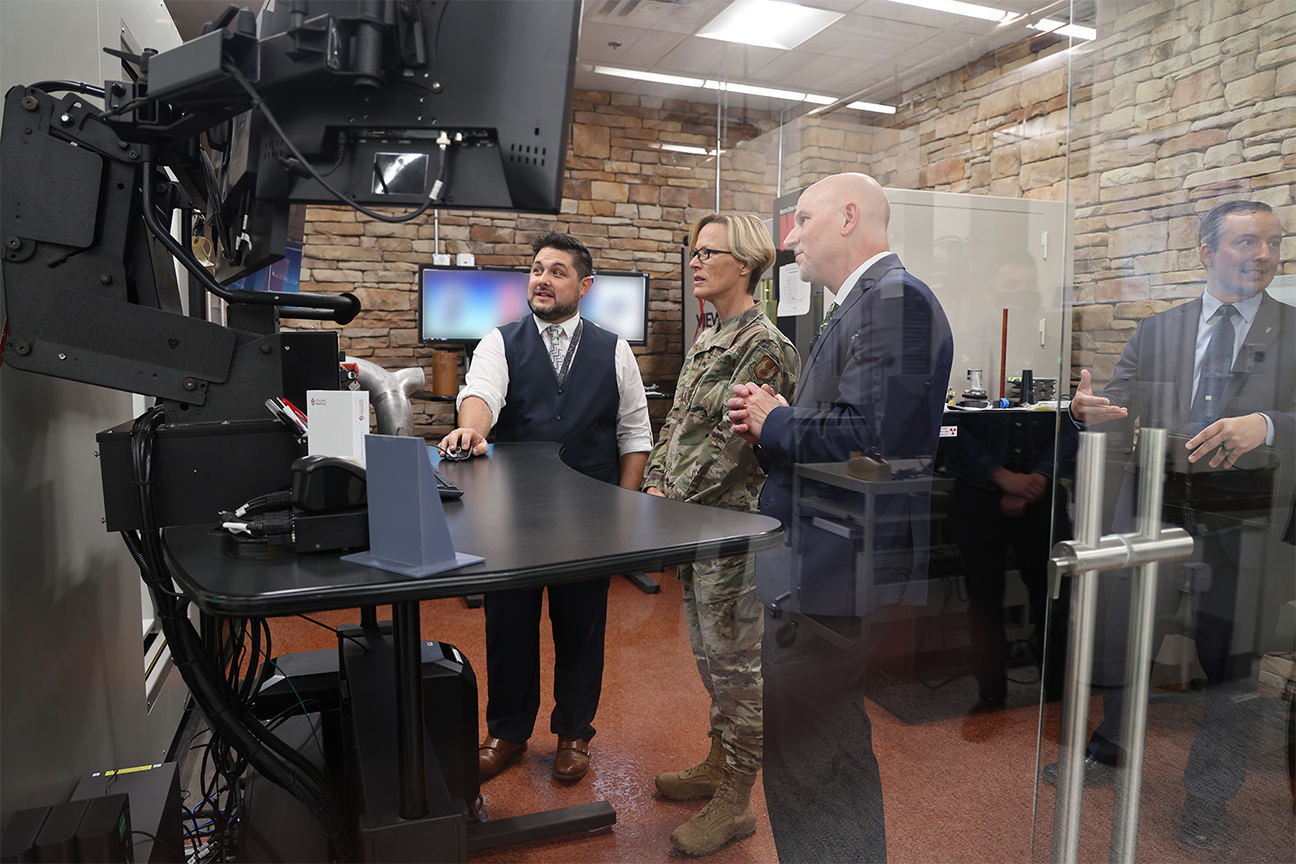
Air Force Research Laboratory Commander Maj. Gen. Heather Pringle receives a tutorial from ARCTOS contractor and Computed Tomography, or CT, operator Chad Schmidt inside the new CT suite Nov. 9, 2022, at Wright-Patterson Air Force Base, Ohio, while AFRL Technical Lead John Brausch and Materials and Manufacturing Directorate Director Darrell Phillipson, far right, observe. The Computed Tomography Laboratory was recently renovated to include an additional CT machine and a brand-new CT suite in which to house the equipment. (U.S. Air Force photo / Jonathan Taulbee)
Thompson explained that the Accelerated Materials and Processing Solutions branch performs mechanical property testing of aerospace-grade materials in several ways, not just via nondestructive CT testing. To be considered airworthy, manufactured components must meet a specific set of very high standards in terms of non-destructive as well as destructive qualities.
“What we do, it’s kind of like a big puzzle. We try to figure out how to put all the pieces together and make them work,” Thompson said. “We look at the active lifecycle of the materials. We ensure airworthiness. Product quality is the goal.”
While non-destructive testing can pinpoint potential defects in materials and test for strength capabilities, destructive testing, by contrast, determines the point at which a component or material fails. Engineers apply different destructive test methods to manipulate, deform or destroy the material completely to better understand how the object’s physical properties respond under pressure and force.
Thompson noted that the lab renovations and the addition of the new CT machine and suite are all part of a major effort to push the current facility beyond the World War II-era and into the future.
Geis, who supported the facility redesign efforts and managed the renovation project, said that maintaining a world-class research and design enterprise “not only requires the brightest minds and state-of-the-art equipment and programs, but also modern and reliable infrastructure.”
“With an average facility age approaching 60 years old in RX, what we increasingly find is that the infrastructure is a limiting factor to the research,” Geis said. “We need quick and responsive execution of large recapitalization efforts like this to remain relevant.”
To that end, Geis explained, the facility was refurbished with brand-new flooring, ceilings, lighting and fresh paint.
“This allows us to perform our mission in a little bit of a nicer environment,” Thompson said, noting that workplace modernization efforts can translate to even higher levels of employee motivation, creativity, and job satisfaction.
For Thompson, who got his initial start in the Materials and Manufacturing Directorate in January 1985 as a cooperative education intern, the upcoming completion of the project is “a bit of a personal accomplishment.”
Thompson, who plans to retire next year, said: “It’s an example of leaving a place a little bit better than I found it.”
About AFRL
The Air Force Research Laboratory, or AFRL, is the primary scientific research and development center for the Department of the Air Force. AFRL plays an integral role in leading the discovery, development, and integration of affordable warfighting technologies for our air, space, and cyberspace force. With a workforce of more than 11,000 across nine technology areas and 40 other operations across the globe, AFRL provides a diverse portfolio of science and technology ranging from fundamental to advanced research and technology development. For more information, visit: www.afresearchlab.com.