AFRL eyes development of next-generation textile for DAF uniforms
WRIGHT-PATTERSON AIR FORCE BASE, Ohio (AFRL) – The Air Force Research Laboratory, or AFRL, has partnered with the Air Force Life Cycle Management Center, Cornell University, Ohio-based contractor UES, Inc. and the Palmer Muskox Farm in Palmer, Alaska to explore the use of synthetic muskox wool keratin fibers in textiles for military-grade uniforms. The International Cooperative Engagement Program for Polar Research, or ICE-PPR, a collaboration between the United States and various partner nations to improve defense and security capabilities in the Arctic region, inspired nascent research efforts, while the Office of Naval Research, AFRL chief scientists and AFRL Core Programs supplied funding for the project.
Initial research conducted in AFRL’s Materials and Manufacturing Directorate and the 711th Human Performance Wing indicates that raw muskox wool fibers — a material also known by the indigenous term qiviut — are preferred for their ability to lend enhanced thermal insulating properties to textiles. When combined with other natural or synthetic polymers such as nylon through a process called electrospinning, qiviut can potentially be used to create an alternative textile that is lighter, stronger and more environmentally sustainable than the merino wool cold-weather garments traditionally fielded to Airmen and Guardians for Arctic-based missions.
More recently, researchers in the Materials and Manufacturing Directorate’s Biomaterials branch have set their sights on recreating muskox wool keratin fibers in the lab using synthetic biology to address theoretical supply chain needs, prioritize U.S.-based textile manufacturing and promote biotechnology research initiatives in the U.S.
“There is a need for uniform improvement when it comes to the Arctic strategy,” said Dr. Nancy Kelley-Loughnane, research team lead in the Materials and Manufacturing Directorate’s Biomaterials branch. “When pilots conduct cold-climate missions in Arctic spaces such as Alaska, they might need to land in water, on frozen tundra, on ice. There are a multitude of possibilities. So, we need a textile that has multiple properties, something that does more than just keep us warm in the event of unplanned isolation.”
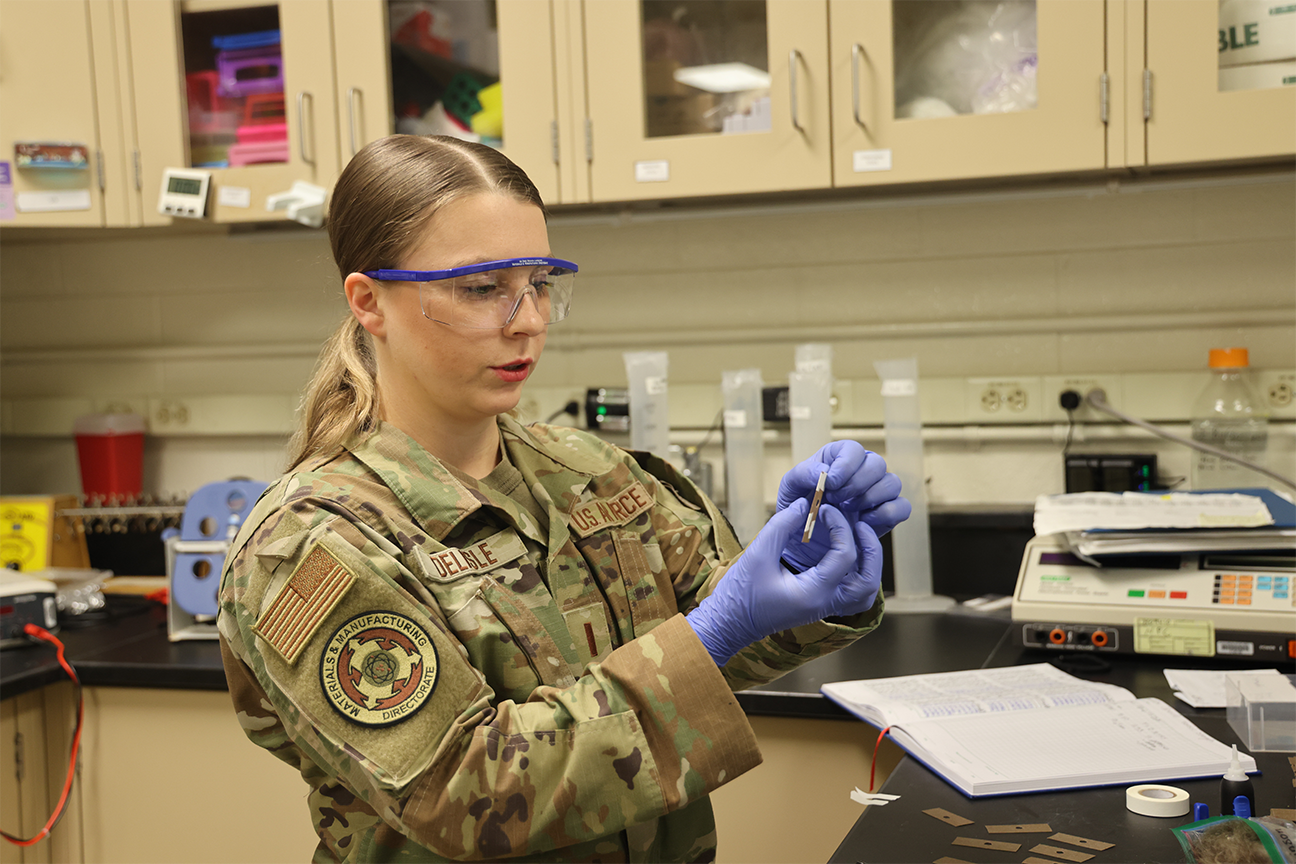
2nd Lt. Evon Delisle, a Biomaterials Research Scientist, prepares muskox guard hair samples to test their break force, or load that the material can sustain before breaking, in the Air Force Research Laboratory, or AFRL, Biomaterials Laboratory of the Materials and Manufacturing Directorate, Wright-Patterson Air Force Base, Ohio, May 12, 2023. Researchers involved in this facet of the muskox wool keratin fiber project seek correlations between animal age, fiber diameter and break force, and examine how those characteristics are associated with different keratin genes. (U.S. Air Force photo / Jonathan Taulbee)
The ideal cold-weather textile would offer thermal insulating, quick-drying and moisture-wicking properties and would remain reasonably lightweight in the event of water immersion, said Dr. Mark Tyler Nelson, research biomedical engineer in the 711th Human Performance Wing.
While more traditional materials such as merino wool and goose down have typically been used to insulate cold-weather garments, they raise a variety of concerns about practicality and sustainability, Nelson said.
“Most of the cold-weather garments that the United States military uses are simply not graded to a level as cold as the Arctic might get,” Nelson said. “For a while, goose down filler was sort of the gold standard in terms of providing warmth, but there are a lot of ethical concerns surrounding its utilization. It is also ineffective if it gets wet. The other common alternative, merino, dominates the wool industry, but it’s expensive.”
Merino wool is costly in part because the vast majority — roughly 81% — is imported to the United States from Australia, said Dr. Braden Li, materials science engineer and textile expert in the Air Force Life Cycle Management Center, or AFLCMC. Merino also becomes impracticably heavy when wet, Li said.
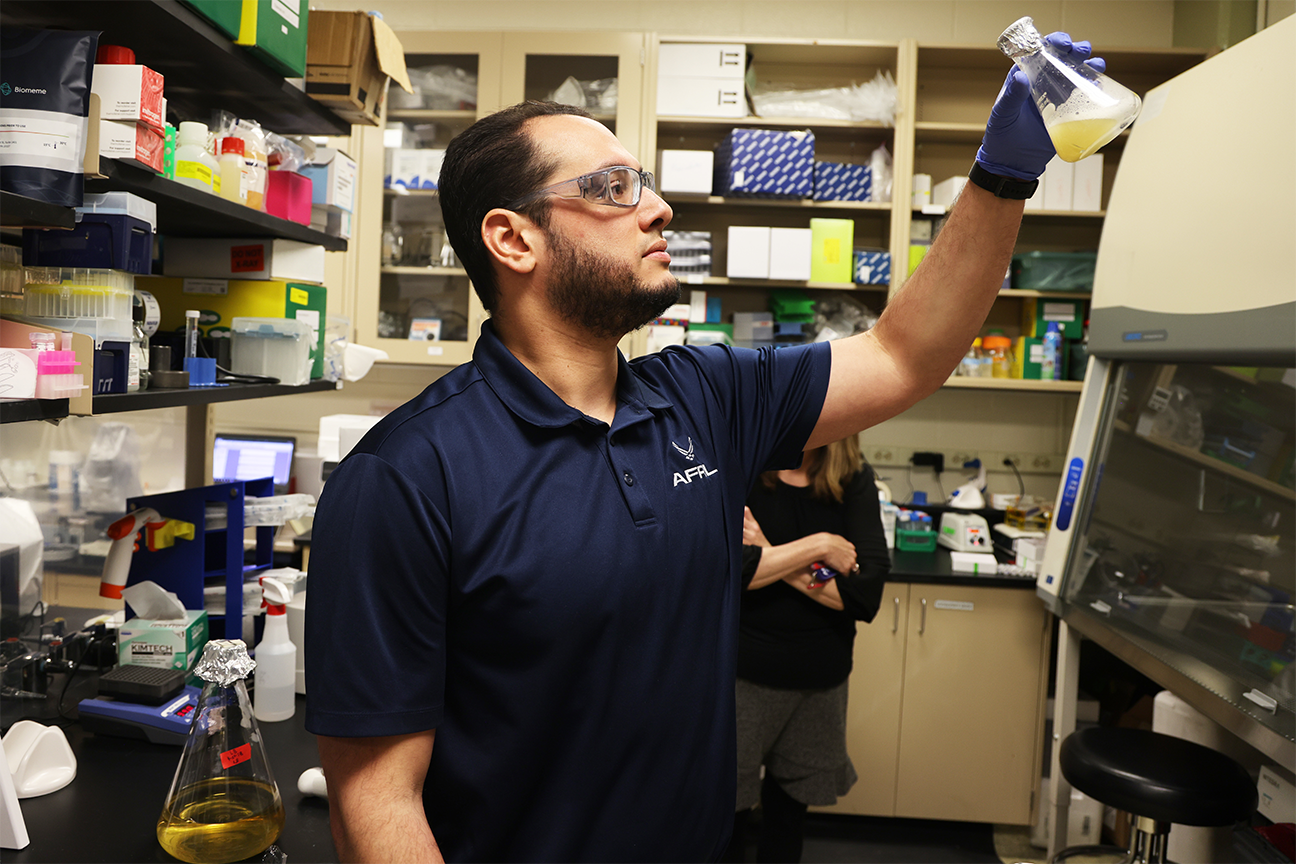
Biomaterials Research Scientist Dr. Victor Roman examines the density of overnight saturated bacterial cultures in a small flask that was used to “seed” larger volumes of cultures in the Air Force Research Laboratory, or AFRL, Synthetic Biology Laboratory in AFRL’s Materials and Manufacturing Directorate, Wright-Patterson Air Force Base, Ohio, May 10, 2023. “Seeding” is the first step in prepping cultures for keratin expression, and the smaller flask contains a bacterial strain engineered to express a particular muskox keratin protein. Culture density is an indicator of healthy bacterial growth, Roman said. (U.S. Air Force photo / Jonathan Taulbee)
“Traditionally, the gear that is fielded to our pilots and aircrew is not fitting the bill just yet,” Li said. “It just is not designed to work in an Arctic environment. Yes, it might keep you warm, but it’s so bulky and cumbersome.”
It is tricky to balance all of the desired properties in a cold-weather military-grade textile, Li added.
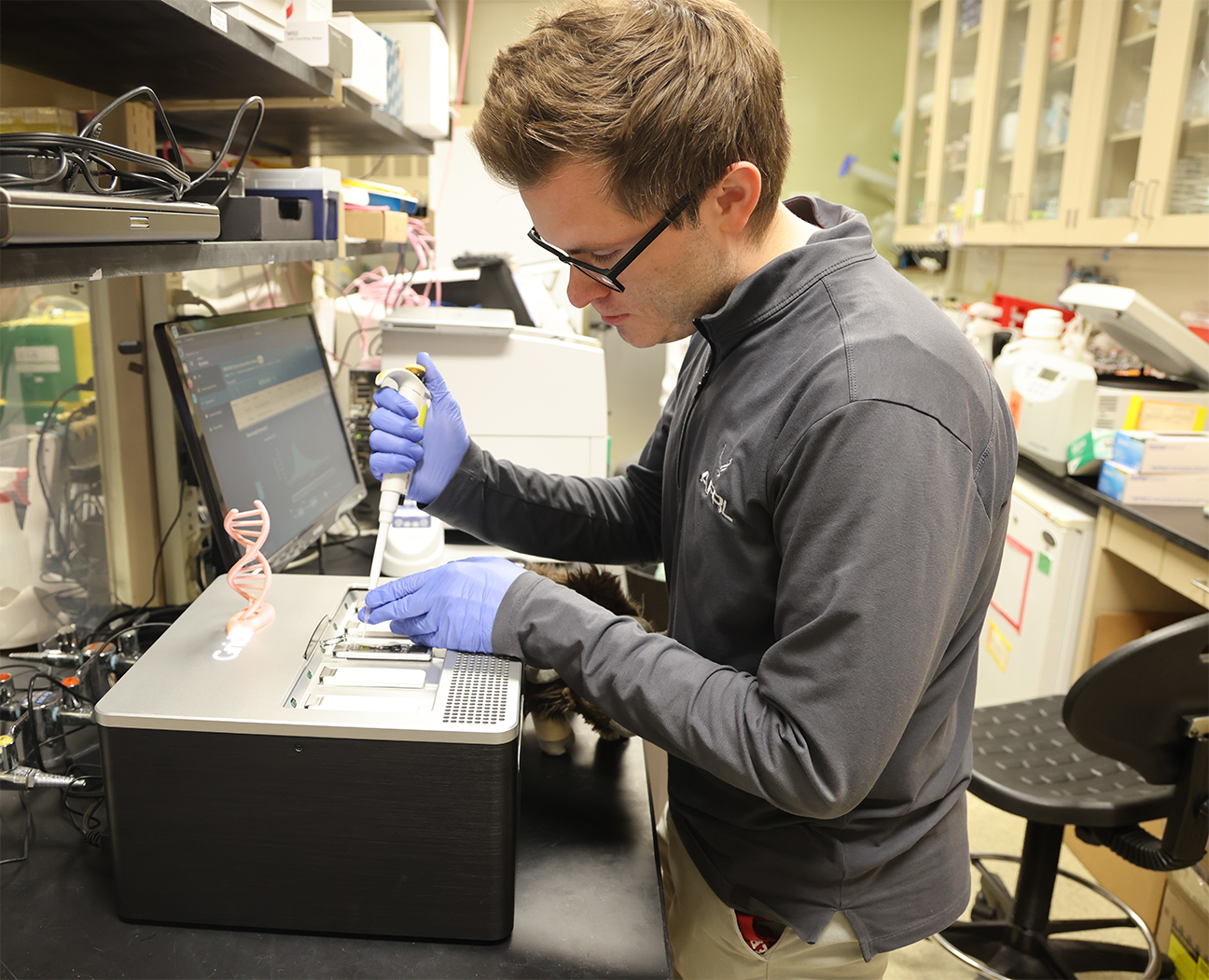
Bioinformatics Team Lead Dr. Blake Stamps pipettes biological samples for use in a DNA sequencer, an instrument that researchers in the Air Force Research Laboratory, or AFRL’s, Materials and Manufacturing Directorate use to read DNA samples and generate high-quality electronic data pertaining to the muskox genome, in the Synthetic Biology Laboratory at Wright-Patterson Air Force Base, Ohio, May 10, 2023. Scientists are most interested in the genomic information most closely associated with the thinness of muskox wool fibers, as thinner fibers provide greater thermal insulating properties. (U.S. Air Force photo / Jonathan Taulbee)
“We don’t want the Airmen so weighted down that they can’t go anywhere,” Li said. “We want the fabric to be breathable because if they start sweating in all of this heavy clothing, as soon as they take it off and get hit with an Arctic chill, they can get frostbite, maybe even freeze to death. So, it’s a matter of balancing thermal insulation with sufficient weight, dexterity and breathability. Muskox wool keratin has the potential to allow us to create a textile that offers all of those properties.”
Another aspect of the project that researchers are considering is how to keep textile production for military uniforms in the United States to reduce reliance on foreign nations, as most industrial textile manufacturing has long since moved overseas, Li said.
In the event of potential conflict, the U.S. government will require access to a steady, controllable domestic textile supply chain in order to fulfill both military and civilian clothing needs. The Berry Amendment, originally passed by Congress in 1941 as part of the Appropriations Act, became permanent in 1994 and required the DOD to give preference in procurement to items produced in the United States, particularly clothing and fabrics, according to the Assistant Secretary of Defense for Acquisition website.
While qiviut shows strong potential to fill in as an alternative textile to help meet future DAF uniform needs, it, like merino, is expensive to source, and due to limited herds, an adequate supply chain of domestic muskoxen wool is not feasible.
“In the wild, an Alaskan muskox only produces maybe one offspring every one to three years — perhaps more on a domesticated farm,” said Dr. Heather Jay Huson, animal geneticist and associate professor in Cornell University’s Department of Animal Science.
Huson has collected biological DNA samples from a herd of domesticated muskoxen housed at the Palmer Muskox Farm for her own research for more than 15 years. Through a contract with AFRL, Huson provided samples of raw muskox wool to researchers in the Biomaterials branch, who tested the material to establish that its thermal insulating properties are analogous to merino.
“It is not a secret that when you compare qiviut to merino sheep’s wool, muskoxen have finer, stronger fiber that is at least as warm, if not warmer, than merino, which makes it an ideal cold-weather material,” Huson said. “But muskoxen populations are limited.”
Resources and access provided by the Palmer Muskox Farm and its executive director Mark Austin have been critical in terms of enabling the research, Kelley-Loughnane said.
The care and keeping of domesticated herds of muskoxen also requires access to ample land mass in the cold, dry, high Arctic climate, the species’ natural habitat, said Dr. Blake Stamps, Bioinformatics lead and research biological scientist in the Biomaterials branch.
“We are not going to be able to breed and feed these animals just to make military uniforms — that is just not practical,” Kelley-Loughnane said. “So, eventually, the question became: well, can we manufacture this product ourselves — and can we do so practically, affordably, sustainably, with a good return on investment for the Department of the Air Force?”
That’s where synthetic biology comes into play, Stamps said.
The research team’s focus ultimately shifted to how they might recreate a synthetic version of qiviut — a material that could essentially mimic all the preferred qualities of natural muskox wool fibers — by recombinantly expressing muskox fiber proteins in E. coli bacteria.
“It’s a fermentation process, similar to brewing beer,” Stamps said. “Our scientist essentially isolated the keratin gene, one of the structural components of that muskox fiber, and then another scientist took that and stuck it into a bacterium, and E. coli is making it now. We can ferment synthetic muskox keratin fiber in bacteria, purify it, and get that material over to the electrospinning scientists [in the 711th Human Performance Wing].”
Researchers can potentially use the electrospinning process to tinker with the properties of the synthetic material, combining it with other preexisting polymers such as nylon, to arrive at a preferred textile product that meets specifications for warmth, weight, dexterity and breathability, Stamps said.
The first step in this process was to complete genetic sequencing on a series of approximately 20 blood and saliva DNA samples that Huson obtained humanely from the muskoxen at the Palmer Farm to create a complete genome for the muskox species, said Dr. Dominique Wagner, computational research scientist in AFRL’s Biomaterials branch.
Wagner used the DNA samples that Huson supplied to create a genetic reference assembly, or digital representative example of a specific species’ set of genes. Wagner’s reference assembly was created by piecing together the genetic sequences from a single muskox that was sequenced at much greater depth than the other 19 animals to make a muskox genome that was as continuous and complete as possible.
Next, Wagner singled out the specific keratin and keratin-associated proteins that would be most desirable in a synthetic material.
“In the Muskox genome, there are more than 90 keratin and keratin-associated proteins associated with fiber production,” Wagner said. “But the six or eight of those that we are most interested in are the ones associated with the creation of the thinness of the fiber. The thinner the fiber, the better the thermal properties are, the more insulating it is.”
Wagner supplied this genetic information to Research Scientist Dr. Victor Roman in the Biomaterials branch, who used molecular tools such as Polymerase Chain Reaction, or PCR, and standard cloning techniques to insert a specific piece of genetic information into what is known as a bacterial expression vector — in this case, E. coli bacteria.
“Once we express the keratins in the bacteria, we use a method called affinity purification, which allows you to isolate just the proteins you want that the bacteria are producing,” Roman explained. “It’s like going fishing. We use a particular bait, in this case nickel beads, because these keratins have a polyhistidine tag [an amino acid motif in proteins] that binds to the nickel beads — and you use them to fish out the keratin from bacterial lysates.”
From there, Roman said, it is simply a matter of cleaning up the keratin proteins and handing off the purified material, now in a powder form, to Nelson and his team in the 711th Human Performance Wing to begin experimenting with the electrospinning process.
“We’re using biology as inspiration, digitizing that biology and then taking it back into the lab and making it into something new, or better,” Stamps said. “One of the thoughts is that perhaps we can use electrospinning to coat preexisting nylon fiber with muskox keratin as a stronger, protective shell. Then, what you could potentially wind up with is this bio-enhanced nylon fiber that we can feed into the military uniform process.”
Dr. Pat Dennis, senior research biologist in the Biomaterials branch who has helped oversee the project, said that his team’s well-balanced partnership with the AFLCMC, Cornell University and the 711th Human Performance Wing has resulted in virtually no duplication of efforts.
“It’s very complementary, what we do, and there’s very little overlap,” Dennis said. “We each have our own distinct roles in making this research happen. It’s been such a huge win for us to have such a cooperative group, spanning multiple directorates and academia, all of whom are so willing to share materials and knowledge and expertise.”
The team unanimously agreed that potential future next steps involve scaling up keratin protein production in the lab and eventually partnering with the textile industry.
“We can do all of the validation on a small scale here,” Roman noted. “And then once we are at a point where we can say, yeah, we can produce large amounts of keratins, then the plan is to partner up with industry and see how they can implement this keratin material into their workflow, in the creation of a new, novel textile with improved features.”
Right now, Stamps said, the creation of synthetic muskox keratin proteins is done in small flasks in the lab, but his team is getting closer to having the capacity to produce the material in larger vessels in industrial-sized amounts.
“Then we have to figure out how to optimize the process and ultimately engage with an industrial partner who wants to actually make it,” Stamps added.
The team’s hope is to eventually arrive at a next-generation textile that not only checks all of the boxes in terms of superior quality and accessibility but also benefits the environment, Kelley-Loughnane said.
“The way we obtain textiles, and the ways in which we currently make clothes, aren’t always very sustainable,” Kelley-Loughnane noted. “Current practices require the use of excess chemicals and petroleum-based products. We are working to find a way to change that.”
Muskoxen, which are more genetically similar to goats than cattle, are one of very few prehistoric animals still in existence today, Huson said, but they became extirpated, or virtually extinct, in Alaska by 1920.
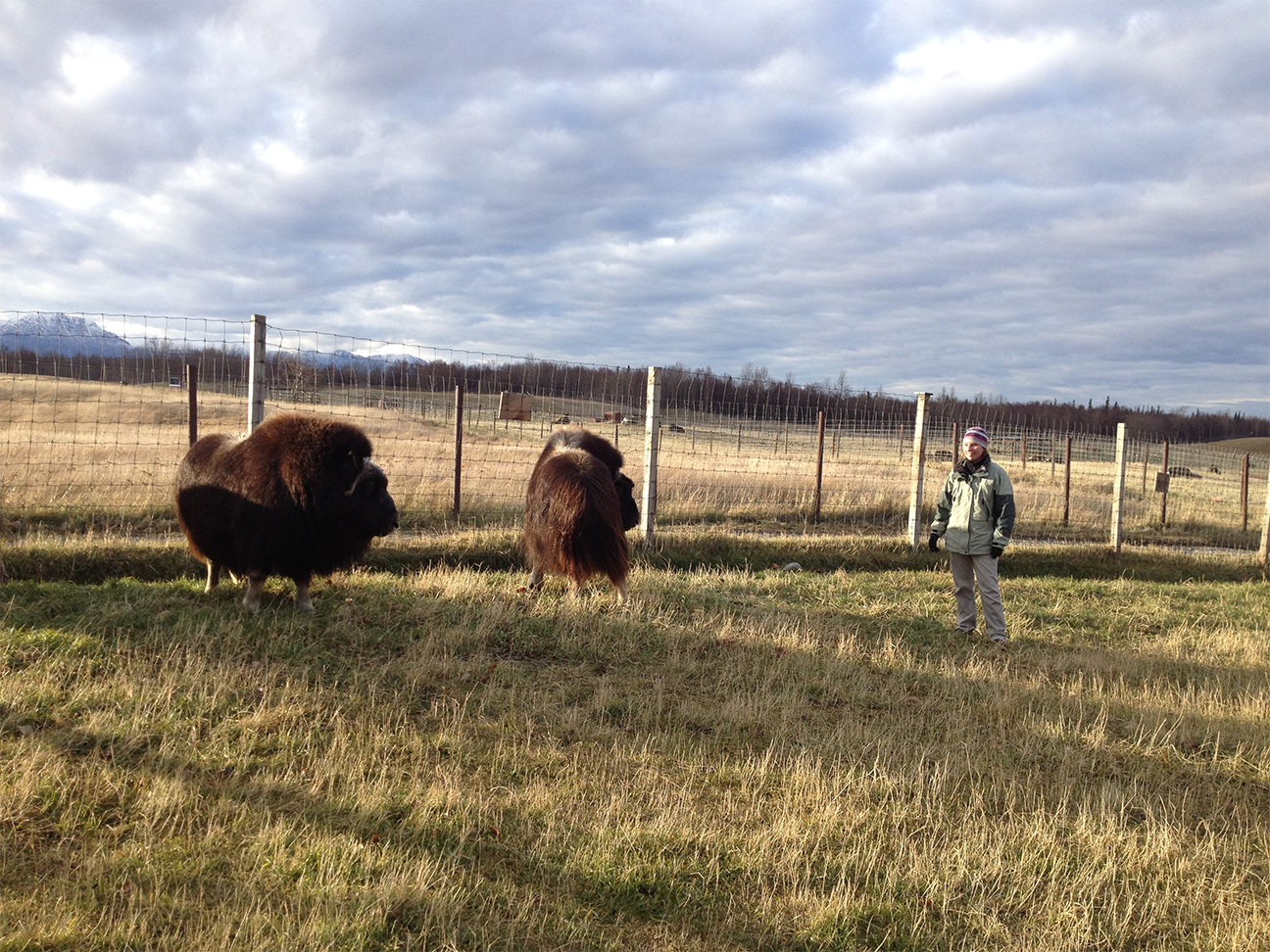
Dr. Heather Jay Huson, animal geneticist and associate professor at Cornell University, stands at pasture with two adult muskoxen at the Palmer Muskox Farm in Palmer, Alaska. Huson has humanely collected biological DNA samples from a herd of domesticated muskoxen housed at the farm for her own research purposes for more than 15 years. Through a contract with the Air Force Research Laboratory, or AFRL, Huson provided samples of raw muskox wool to researchers in AFRL’s Materials and Manufacturing Directorate, who tested the material to establish that its thermal insulating properties are comparable to merino wool. Researchers in AFRL’s Biomaterials branch and the 711th Human Performance Wing are currently testing a process known as electrospinning to blend synthetic muskox wool keratins with preexisting polymer materials, such as nylon, to create an alternative textile that is lighter, more breathable, and more environmentally sustainable for future use in U.S. Department of the Air Force uniforms. (Courtesy photo/ Cornell University)
In 1930, relocation efforts brought a small group of 34 muskoxen by boat from East Greenland to Nunivak Island, a permafrost-covered volcanic island about 30 miles offshore from Alaska, where they were released and allowed to breed naturally, according to the Alaska Department of Fish and Game. From there, a number of these animals were transported to Alaska, where they continued to thrive, although in recent years, their numbers have dwindled somewhat.
The muskoxen wool fiber and keratin protein research has the potential to serve as what Stamps refers to as “bioinspiration,” or a mere jumping-off point for future inquiry into the production of next-generation fabrics and fibers. Stamps’ research team is in the process of requesting additional funding to expand their exploration of how other Arctic animals, such as penguins, polar bears, and Arctic goats, keep themselves warm.
Similar to muskoxen, the hair of polar bears is medullated, or hollow, which plays a role in keeping the animals warm. Scientists are interested in exploring that factor as a potential contributor to the creation of future novel thermal insulating textiles, Dennis said.
“I’m a big fan of biology for its complexity,” Dennis said. “I think that’s probably why we’re all doing this. It’s a field that is just unparalleled in its intricacy. While this research is still in a very early state, what I am most excited about is its potential to inform the next generation of insulative materials that can actually contribute to solving a problem.”
Huson called her partnership with AFRL enlightening.
“It has been really eye-opening for me, as someone who has been conducting animal genetic research for so many years, to see any branch of the military interested in doing biological research like this,” Huson said. “That the Department of the Air Force, and AFRL, are aware of the potential benefits it offers for the future — that’s really exciting.”
About AFRL
The Air Force Research Laboratory, or AFRL, is the primary scientific research and development center for the Department of the Air Force. AFRL plays an integral role in leading the discovery, development and integration of affordable warfighting technologies for our air, space and cyberspace force. With a workforce of more than 11,500 across nine technology areas and 40 other operations across the globe, AFRL provides a diverse portfolio of science and technology ranging from fundamental to advanced research and technology development. For more information, visit www.afresearchlab.com.