AFRL repairs next generation composite materials with light
WRIGHT-PATTERSON AIR FORCE BASE, Ohio – Scientists at the Air Force Research Laboratory and Hanyang University are developing smart structural composites that are robust and photothermally responsive, enabling next generation composite materials that are repairable with the application of light sources.
This is a joint collaboration between the United States and South Korea with participation of AFRL and Hanyang University through collaborative sponsorship of the Air Force Office of Scientific Research and the National Research Foundation of Korea.
“This partnership has helped us to leverage resources and accelerate our technology development,” said Professor Youngjong Kang of Hanyang University.
“We are developing an evolving and transformative materials technology that enables real-time system readiness and cost savings in the area of system sustainment and electromagnetic interference (EMI) shielding,” said Dr. Dhriti Nepal, Research Materials Engineer, of AFRL.
The structural damage repair in traditional epoxy composites is time-consuming and labor-intensive. Component downtime during repair also adds to loss of squadron readiness, in addition to excessive labor-intensive repair cost.
Traditional epoxy thermosets are infusible and unable to be remolded. It is nearly impossible to repair without completely replacing the entire component.
The development of smart photothermally activated composites repair via light activation adaptable to non-invasive (practically eliminating human touch labor) provides a significant breakthrough in sustainment of aircraft systems. This enables exceedingly low-cost repair.
This technology and EMI shielding have the potential to transition the research to system applications to meet warfighter needs.
Vitrimer materials, otherwise known as a class of plastics derived from thermosetting polymers, is one solution to providing a material that will alleviate issues related to mechanical repair. Vitrimer properties can be tailored to incorporate electrospray ionization (high voltage applied to a liquid to create an aerosol) shielding.
“Prime aerospace industry members see an immediate need for this technology for significant cost savings and boosted system readiness,” said Dr. Ajit Roy, Principal Material Research Engineer, of AFRL. “We are excited to experiment on the development of new generation nanoparticles incorporated into composites to meet application requirements for filled elastomer (a semi-flexible polymer that is added in between structural components to fill component gaps and to provide electrical connectivity) and EMI shielding.
To coincide with the development, Dr. Yixin Ren and Dr. Amber Hubbard of AFRL recently participated in a “Science as Art Competition” at the 2020 Spring Materials Research Society meeting.
Ren’s “Carbon Nano Shish Kabob,” showing carbon nanotubes’ growth on carbon fibers, was awarded in the top 50 of the competition.
Hubbard’s “(Thermoplastic) Flower in the Sun,” showing a system that can transform films into 3D shapes based on a photothermal response, won second place.
Fundamental technical challenges remain to be worked to make the technology insertion to Air Force systems happen; however, a cohesive and productive multidisciplinary team is in place to advance this important and scientifically relevant technology.
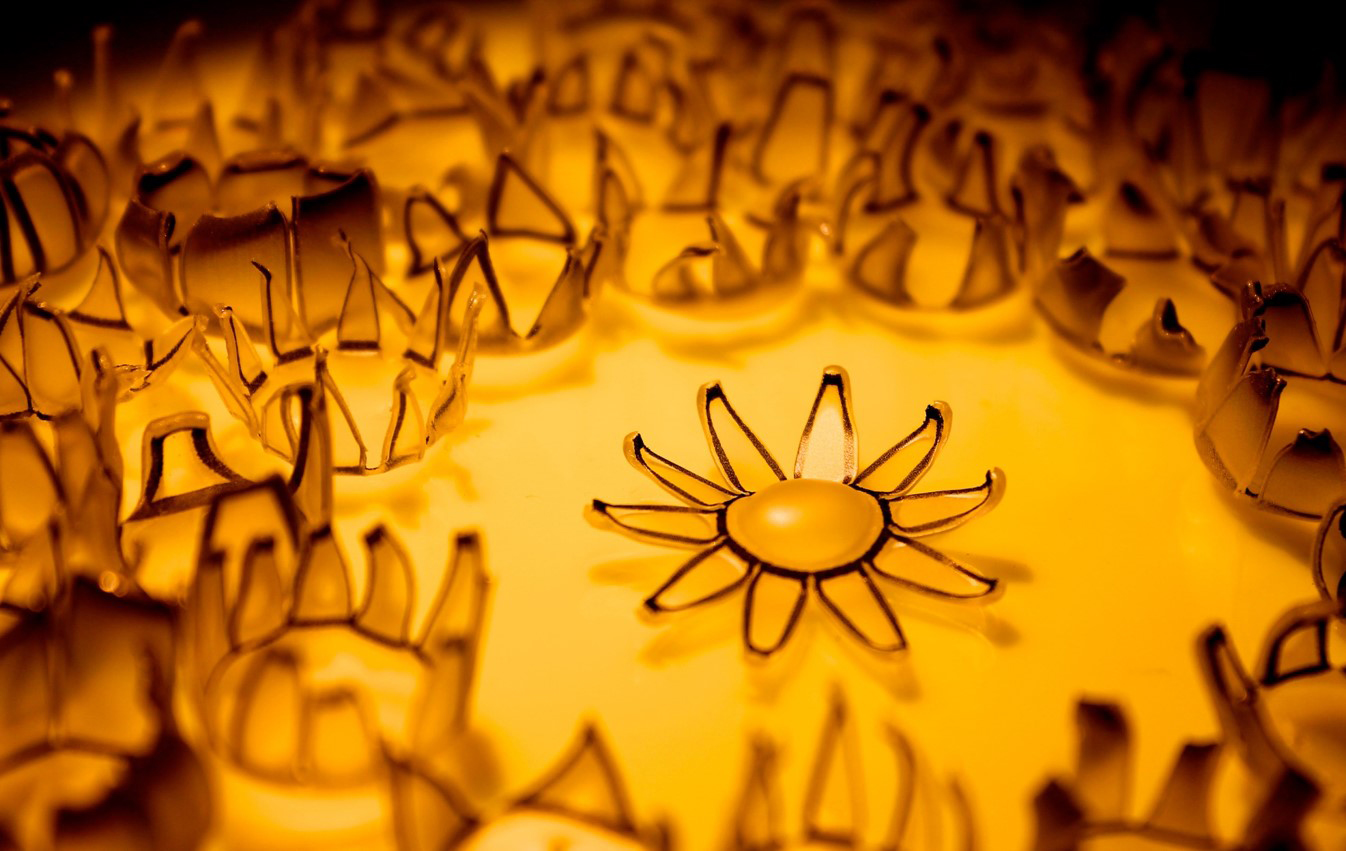
(Thermoplastic) Flower in the Sun. Stimuli-responsive polymers have gained increasing attention for their applications ranging from soft robotic grippers to actuators. By controlling strain within thin thermoplastic sheets, these small grippers can transform into three-dimensional shapes based on a photothermal response and withstand loads more than 24,000 times their own mass. (Courtesy photo/Amber Hubbard)
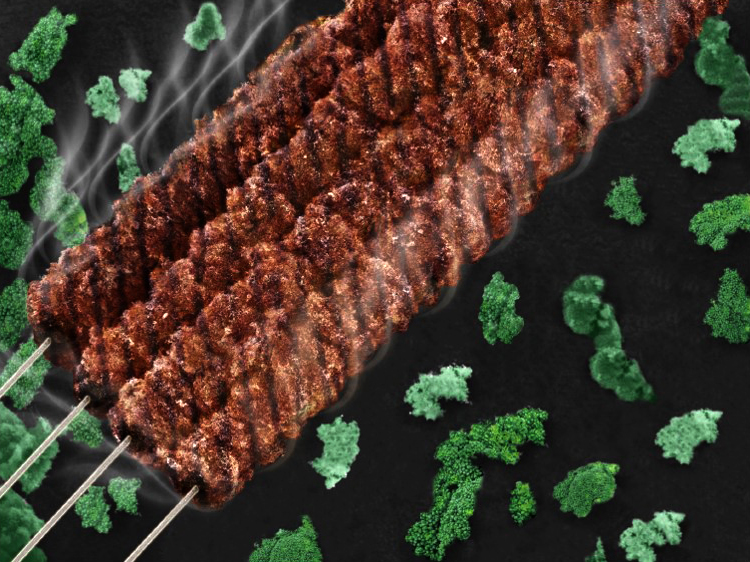
Carbon Nano Shish Kabob. This science as art piece is created by the scanning electron microscope image. Carbon nanotubes were deposited on carbon fibers via chemical vapor deposition method. The overgrowth of carbon nanotubes on carbon fibers created the shish kabob like carbon nanostructure. (Courtesy photo/Yixin Ren)