AFRL, University of Texas – Arlington collaboration yields break-through in thin film technology
WRIGHT-PATTERSON AIR FORCE BASE, Ohio (AFRL) — The Air Force Research Laboratory, or AFRL, recently saw the highly successful conclusion to a collaboration with the University of Texas in Arlington, or UT Arlington, which yielded a significant breakthrough in thin film technology used in infrared light detectors.
“Thin film technology is the basis of the microchips used in most modern electronic devices,” said Dr. Bruce Claflin, a senior research physicist with AFRL’s Sensors Directorate. “In the case of infrared light detectors, a special material is used to absorb the light with the electronic circuitry, which is used to display information to the user.”
He said one familiar way these devices are used, is to measure the distance to nearby objects such as the lane change sensors in cars. The Department of the Air Force uses these infrared detection sensors to map surface terrain and identify ground and airborne targets.
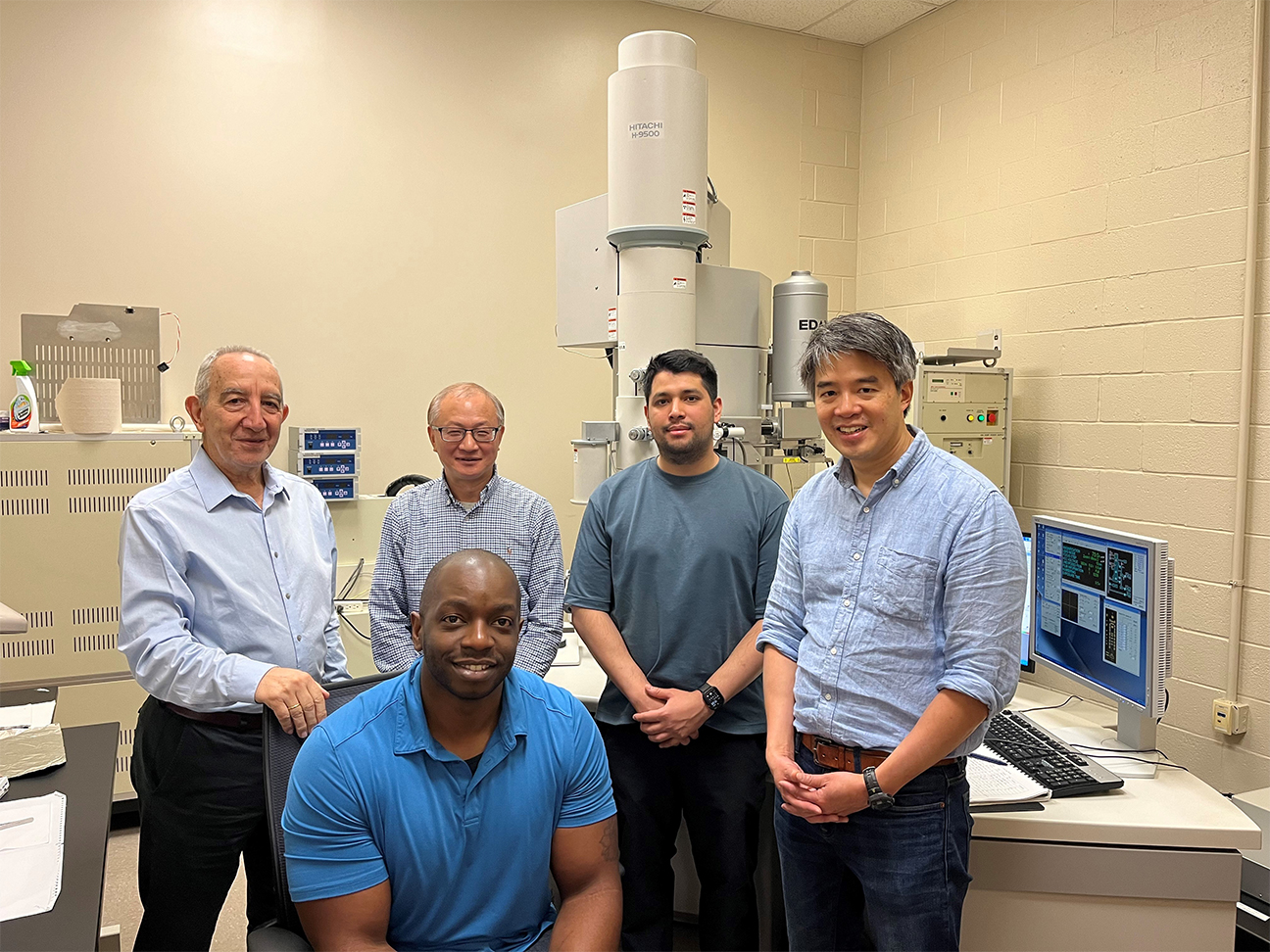
From left: University of Texas in Arlington, or UT Arlington, team members Dr. Stathis Meletis, Dr. Jiechao Jiang, Enrique Ramirez, Dr. Joseph Ngai and Nonso Martin Chetuya gather for a photo at UT Arlington May 16, 2024 to celebrate the successful conclusion to a collaboration with the Air Force Research Laboratory’s Sensors Directorate. The collaboration was made possible through the Minority Leaders Research Collaboration Program and resulted in a significant breakthrough in the development of thin film technology, as a potential lower-cost alternative to be used in infrared light detection. (Courtesy photo / Dr. Yi Shen)
The collaboration between AFRL and UT Arlington was made possible by a grant through the AFRL Minority Leaders Research Collaboration Program, or ML-RCP. It brought together three UT Arlington faculty, Dr. Jiechao Jiang, Dr. Stathis Meletis and Dr. Joseph Ngai, and students Nonso Martin Chetuya and Enrique Ramirez, who began working with Claflin and Dr. Gordon Grzybowski in 2022. Their work surrounded the development of a new, more cost-effective semiconductor thin film for infrared light detection, to be used as an alternative to the current standard material.
The ML-RCP, which is overseen by AFRL’s Materials and Manufacturing Directorate, is a cooperative agreement with The Ohio State University partnered with subcontractor ARCTOS. The program has several agreements in place with Historically Black Colleges and Universities, or HBCUs, and Minority Serving institutions, or MSIs, across the United States. The program enables collaborative research partnerships between AFRL and academia that engage a diverse pool of talent in addressing foundational research challenges in support of the nation’s air, space and cyberspace technology needs.
“The ML-RCP provides immediate benefits to students, faculty and academic institutions, as well as to the government to help build the next generation workforce with the technical skills needed to continue pursuing the Air Force’s mission,” said Dr. Sirina Safriet, AFRL Materials and Manufacturing Directorate STEM team lead and technical program manager, AFRL ML-RCP. “Diversity in the workplace brings unique perspectives, fostering creativity, innovation and better performance.”
According to Claflin, the work performed by UT Arlington students involved measuring and characterizing the crystallinity, or structural quality, of this alternative semiconductor thin film and performing annealing experiments to improve crystallinity. He said that improved crystallinity will enhance this material’s ability to detect infrared light. Annealing is a heat treatment that alters the physical and sometimes chemical properties of a material.
Claflin explained that while current standard material is more effective and widely used, the cost limits the size of the infrared light detector that can be made, as well as the resolution that it can achieve. It is also difficult to integrate into computer circuitry which further increases cost.
“The performance of this new material is unlikely to exceed that of the current standard,” said Claflin. “However, there are applications where the performance trade-offs versus lower costs are acceptable. Because the potential alternative is less expensive, it has the potential for use in things like unmanned attritable aircraft.”
Attritable refers to a new class of unmanned aircraft that are purpose-designed and routinely reusable but built affordably to allow a combatant commander to tolerate putting them at risk.
After an initial kick-off meeting with the UT Arlington team, samples of the material were sent to students for analysis. After about a month, students requested a video meeting to discuss the extensive data they had collected.
The value of data collected far exceeded Claflin’s expectations. It revealed a breakdown in the structural quality of the semiconductor film above a critical thickness. This helped AFRL scientists and engineers resolve several seeming contradictions that had been plaguing them for quite a while. The result of these findings was a modification of the material deposition process during film production, which achieved desired improvements in crystallinity. New samples were sent to UT Arlington and the results were verified.
These results were so significant that Claflin invited the UT Arlington team to present them at an annual workshop he organized on this material system.
Ngai said that working with a program like the ML-RCP is important because it enables under-represented students to engage in cutting-edge research.
“These opportunities are critical to their development, particularly as many under-represented students are first-generation college graduates,” said Ngai.
From an institutional standpoint, Ngai said that it enabled the technical expertise and research capabilities of UT Arlington to be synergistically harnessed with those of AFRL to tackle projects that are important to the Air Force.
“In short, the dual impact of the ML-RCP on education and research enables UTA to be more effective in fulfilling its mission as a university,” said Ngai. “The students, myself and professors Jiang and Meletis have very much enjoyed and appreciated this opportunity to work with Dr. Claflin, Dr. Grzybowski and AFRL through the ML-RCP.”
About AFRL
The Air Force Research Laboratory is the primary scientific research and development center for the Department of the Air Force. AFRL plays an integral role in leading the discovery, development, and integration of affordable warfighting technologies for our air, space and cyberspace force. With a workforce of more than 12,500 across nine technology areas and 40 other operations across the globe, AFRL provides a diverse portfolio of science and technology ranging from fundamental to advanced research and technology development. For more information, visit: www.afresearchlab.com.