Air Force ups the ante on supersonic rain erosion testing
WRIGHT-PATTERSON AIR FORCE Base, Ohio (AFRL) – The Supersonic Rain Erosion Test Rig (SuRE) at Wright-Patterson Air Force Base is experiencing a full control system replacement and upgrade to provide pinpoint control and unmatched testing value.
The SuRE is used in the evaluation of structures and coatings under the effects of high speed flight through rain for transonic and supersonic speeds up to Mach 2.3. Various high-speed components and coupon specimens such as radomes, leading edge materials, and window materials are tested. Data gathered is essential to field feasible material solutions for weapon systems to operate safely under such environmental conditions.
The only other method to reach this speed for component testing is with a rocket sled or flight testing, both of which are expensive and time consuming. The SuRE provides a cost effective, rapid method to gather data on component performance, tightening the materials development cycle.
The organic improvements underway include features to introduce flexibility in the executed erosion pattern, replace the current control hardware with a highly adaptable and capable LabVIEW (type of control hardware and software platform from NITM) interface and automate secondary operations.
Additionally, improvements to the full control system are expected to save approximately $40,000 annually in sustainment cost, reducing the manpower required to run a test by one-third and maintenance downtime by 25%.
“This has been a great opportunity to apply a personal interest in control and automation to a very powerful tool,” said 1st Lt. Tyler Despard, lead engineer for the upgrade. “I am excited to deliver the final product for use by the organizations that test with us and confident that they will find a renewed value in testing with the SuRE and enjoy the new flexibility to tailor their exposure plan to exact patterns and speeds. I am grateful to the Corrosion and Erosion Team for entrusting me with this responsibility and providing the resources necessary to make this a one-of-a-kind, world-class facility.”
“The rig upgrades are really taking shape,” said Dr. Matthew Hartshorne, Erosion Area Lead. “With two out of three phases complete, we were able to put the control and automation upgrades to the test during a recent run. The control system performed very well and the advantages of modernizing the rig to current technology were evident. We were able to change operating parameters on the fly and monitor the system from a central station instead of walking around the large rig to individual gauges. I am excited to offer the final product to our customers. The team has done a great job making this happen, all during the COVID-19 restrictions.”
The SuRE was initially developed under a small business innovative research contract by Continuum Dynamics Inc., and has since been extensively upgraded by the U. S. Air Force and the University of Dayton Research Institute to increase its available speeds, droplet sizes and specimen throughput.
Numerous systems have already benefited from the SuRE, including Air Force missiles, Navy propellers and commercial space launch vehicles.
The SuRE is operated by UDRI as part of the larger AFRL Impact Erosion Test Facility. A Cooperative Research & Development Agreement with the U. S. Air Force allows UDRI to provide easy access for commercial and government customers. Full-service testing is provided to dozens of joint, international, and commercial customers each year.
To learn more about testing, visit https://udayton.edu/udri/capabilities/materials/rain_erosion.php.
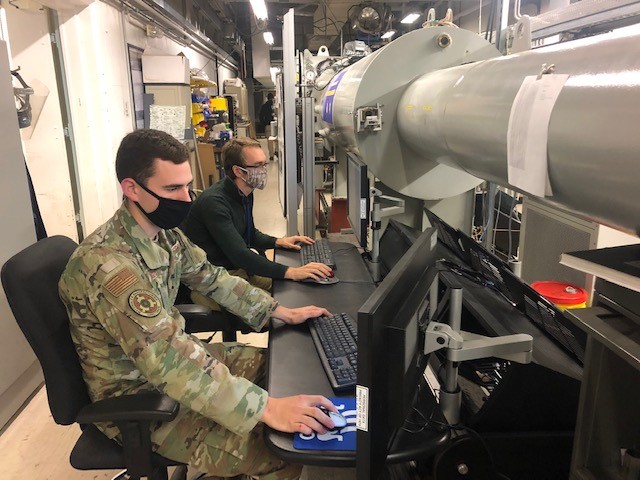
1st Lt. Tyler Despard (front) and Kameron Hayes monitor testing on the Supersonic Rain Erosion test rig. (U.S. Air Force photo/Greg Lanchman)
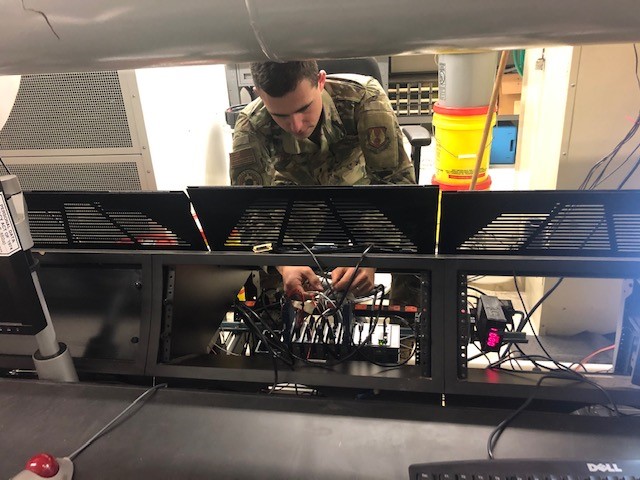
1st Lt. Tyler Despard works on hardware upgrades to the Supersonic Rain Erosion Test Rig. (U.S. Air Force photo/Greg Lanchman)