RE-ARM
SOLID ROCKET MOTOR MANUFACTURING TECHNOLOGY TO REDUCE THE COST AND SCHEDULE OF ENERGETICS / TACTICAL ROCKET MOTOR DEVELOPMENT AND MANUFACTURE
NEW APPROACH TO MANUFACTURING SOLID ROCKETS
AFRL’s Rapid Energetics & Advanced Rocket Manufacturing (RE-ARM) program is developing inexpensive Solid Rocket Motor (SRM) production equipment enabling revolutionary, affordable, flexible, scalable capability to produce state-of-the-art SRMs to support national defense needs. This approach enables affordable expansion of the industrial base, with both current and emerging partners.
ANATOMY
- Emerging Ingredient Synthesis and Propellant Mixing Technologies: Precision generation of propellant ingredients, lower property variance and Reduced propellant processing time.
- Additive Manufacturing: 3D printing of fuel grains enables compositional gradients, integration of performance-enhancing features, and in-situ curing.
- Case-on-Propellant Processing: Direct installation of rocket structural case onto propellant accelerates production and eliminates manufacturing tooling.
- Automation: Robotic staffing of factory eliminates need for human labor, improves process control, and enhances operational safety.
- Non-Destructive Evaluation: The use of comprehensive imaging tools and aids in construction of digital twins for manufactured rockets.
- Digital Engineering: Computational design of requisite rocket aids in prediction of as-built system and provides governance over automated fabrication.
- Stakeholder Collaboration: Teaming with government and industry to accelerate development, qualification, and flight demonstration of RE-ARM technologies.
KEY BENEFITS
- Mature and expand affordable SRM Industrial Base supports requirements for 21st century competition and conflict.
- Rapid design, development, and fielding of new systems helps the U.S. meet emerging threats.
- Flexible manufacturing expands the design space and performance of solid rocket propulsion.
EXPANDED PARADIGM IN ROCKET & WEAPON PRODUCTION
Affordable, small manufacturing centers for SRMs and weapons ensure continuity of necessary force application capabilities for warfighters before and during conflict by enabling affordable production, lowered industrial base barriers of entry, and addressing raw material obsolescence, RE-ARM will prove beneficial to several key Major Commands including Air Combat Command, Pacific Air Forces, US INDO Pacific Command, and Air Force Life Cycle Management Center.
Current rocket propulsion systems of air-launched missiles can take years to enter full rate production due to iterative design, build, and test methods practiced by industry. Furthermore, the U.S. industrial base has consolidated into just a few manufacturing centers for bombs and missiles. Meanwhile, our adversaries’ capabilities have significantly improved in the last decade. REARM is key to avoiding potential strains placed on our nation’s ability to provide timely, sufficient and suitable weapons to the warfighter in future conflicts.
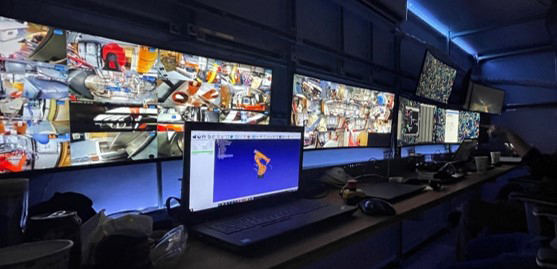
RE-ARM demonstration. Control center and display from X-Bow
Systems RE-ARM inert demonstration, capable of producing inert solid rocket motor propellant grains. Credit: X-Bow Systems.
- Design: Digital Engineering tools accelerate high fidelity, integrated design and analysis. Advanced manufacturing expands design space and potential capabilities.
- Prototype: RE-ARM enables rapid, low-cost prototyping with exquisite or bespoke tooling required, accelerating development cycle.
- Test: Low cost, rapid test to be demonstrated under RE-ARM contracts. Incorporating extensive NDE and DE makes test events more valuable, leading to fewer being required: test campaign is shorter and cheaper.
- Manufacture: RE-ARM enables flexible, less costly production to meet evolving needs by eliminating exquisite and bespoke tooling and significant manpower requirements.
PARTNERSHIP
AFRL’s in-house team has laid the technological ground-work necessary to make RE-ARM a reality. Now, AFRL is collaborating with government and industry partners to accelerate development and transition the capability to the warfighter. The team brings together established defense contractors with emerging aerospace companies.
GETTING INVOLVED
IPT membership is open to all stakeholders (or potential stakeholders) that are eligible to receive Distribution C information (U.S. Government agencies and their contractors).
Applicable white papers are considered through the AFRL Rocket Lab Hermes BAA (FA9300-20-S-0001), a two-step open BAA.